複雑な パイプアセンブリ の製造 全体像の把握の重要性
製造業は、 製造工程の無駄を省き、 コストを削減する方法を常に考えています。 パイプファブリケーターも同じです。 これは、 パイプアセンブリ を構築するために複数のパイプが必要な場合に、 より顕著になります。
パイプ加工業者が直面する最も厄介な課題の1つは、 パイプ部品の接合です。 はめ込み、 固定、 組み立てに困難が伴うことが多いのです。
特に、 曲げ加工後にコーピングやミッタリングなどの二次加工が必要な場合は、 その傾向が顕著です。
例えば、 ある高級フィットネス機器メーカーが新しい有酸素運動用製品 (ここではSTEPと呼ぶ) を開発した場合を考えてみましょう。 この製品は、 長さの異なる9本のステンレス鋼管 (1本のメインパイプと8つの個別部分) で構成される複雑なアセンブリです。 そのため、 一般的な曲げパイプの側面にコープパイプの端部を溶接する必要があります。
この工場には、 機械加工賃の低い旧式の技術と、 最新のパイプ加工装置の両方が設置されています。 メーカーは、 この製品を製造するために最も費用対効果の高い方法を決定する必要があります。
旧式の設備を使用する場合、 メーカーは9本のパイプを指定された形状に個別に加工する必要があります。 曲げ加工の総時間は約3分です (表1) 。
曲げ加工が終わると、 パイプを複雑な冶具で固定し、 フライス盤とマイターソーの工程に入ります。 表2に示すように、 9つのパーツを加工し、 製材するのに約4.4分かかることになります。
はめあいを最適化するためには、 より複雑な冶具が必要となり、 その結果、 冶具のコストが増加する。 時間当たりの機械コストは低くなりますが、 この方法では労働時間と材料消費量が増加し、 製造されるアセンブリの1個当たりのコストが高くなる可能性が高くなります。
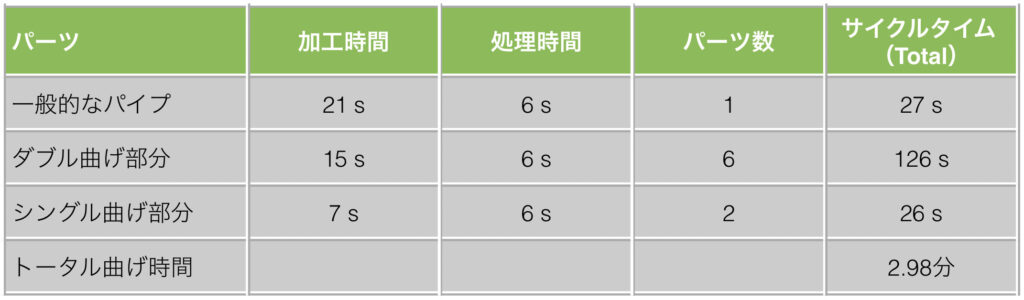
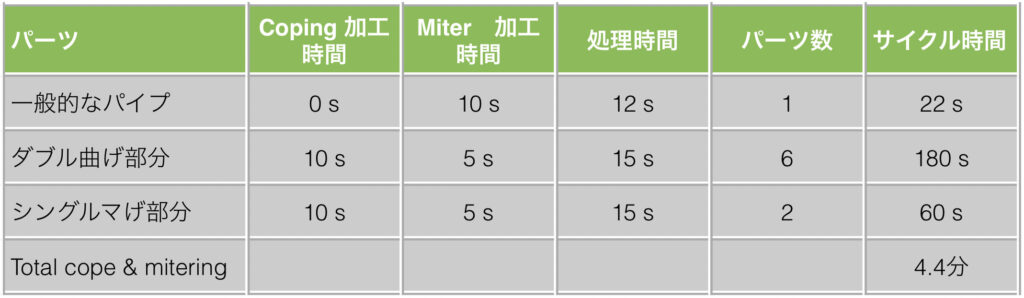
工場が新しい機械で部品を生産することを決定した場合、 パイプレーザーシステムから始めることで、 プロセスを簡素化し、 より効率的に達成することができる、 対処のための最も効果的なソリューションである。 アセンブリCADモデルをパイプレーザープログラムソフトウェアにインポートし、 そこで9本のパイプに個別に分解し、 それぞれの切断フィーチャーを特定することが可能である。
そして、 アセンブリソフトはパイプの組み合わせに基づいてネストを作成する。 この例では、 複雑なアセンブリが9本から3本の材料に最適化されている。 プログラマーは、 マウスを数回クリックするだけで、 タブ、 スロット、 マイクロタブを追加してアセンブリをすばやく最適化し、 アセンブリプロセスを簡素化し、 必要な固定具を最小限に抑えることができます。
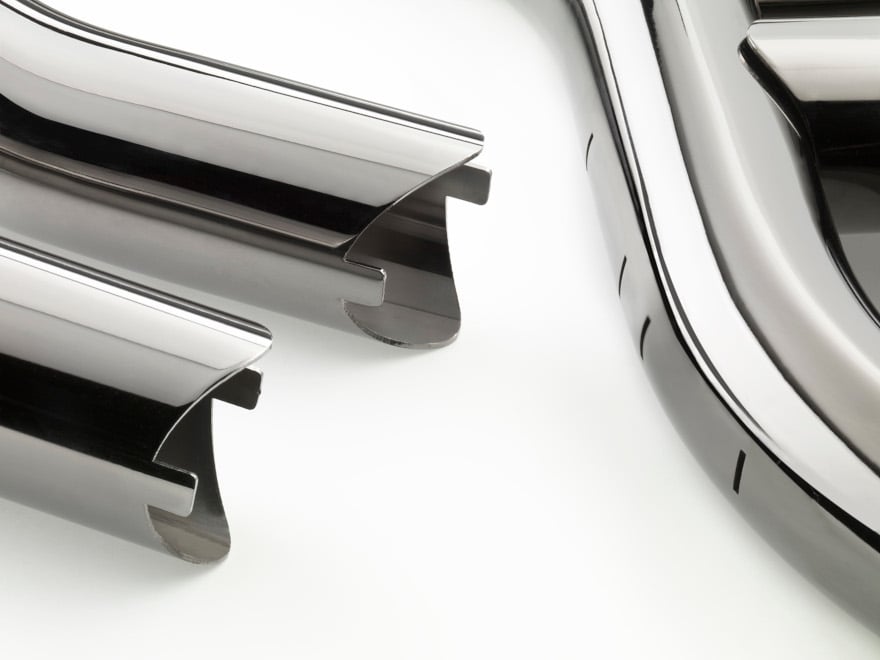
切断の前に、 コーピングと曲げ加工の一部として、 伸びやスプリングバックなどの変数を考慮する必要がある。 旧式の装置では、 最新技術を使ってこれらの要因を特定するために、 曲げ機でプログラムを作成し、 既知の長さのステンレス鋼のサンプル棒から浅い曲げ、 中程度の曲げ、 深い曲げを組み込んでいる。 曲げられたサンプルは、 成形中にどの程度スプリングバックやストレッチが発生するかを特定するために測定されます。 部品の公差が重要な場合は、 材料バッチが変わるたびに評価を行い、 補正の必要性を正確に把握する必要がある。
VGP3Dプログラミングソフトウェアによるパイプ曲げ加工の簡素化については、 こちらをご覧ください!
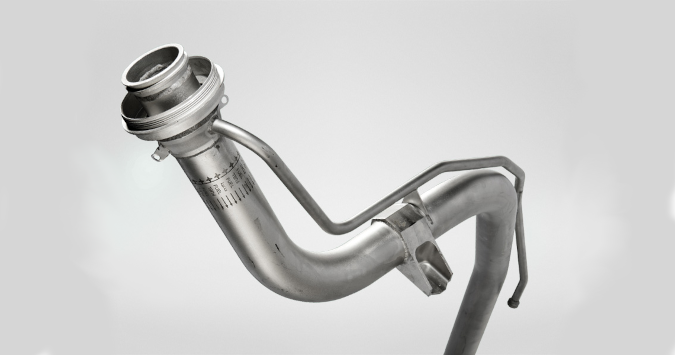
このデータは、 パイプレーザーとベンダーの両方のソフトウェアプログラムで使用できるように保存されます。
パイプレーザーのオペレーターは、 これらの伸縮特性やスプリングバック特性を切断プログラムに組み込み、 各パイプが適切な長さに切断されるようにこれらの要因を自動的に補正する。 これで材料は3つの長さに切断できるようになり、 所要時間は約1.5分です (表3) 。 鋸で切断する場合と比較すると、 生産性は約3倍向上しています。
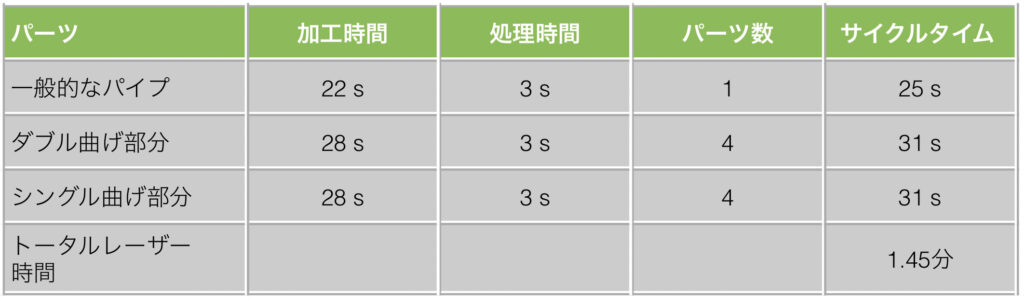
切断から、 パイプは曲げ工程に入りますが、 これはCNC制御の全電動式多軸パイプ曲げシステムで最も効果的に行われます。 元のCADモデルをパイプ曲げのプログラミングソフトに取り込み、 補正データをプログラムに合成する。 加工する部品は9つあるが、 今は3本の棒状の材料だけです。
曲げ加工プログラムを順番に実行することで、 部品は順次生産され、 STEPアセンブリに必要なすべての部品が得られます。
3本のパイプを加工するサイクルタイムは1.6分となり (表4) 、 生産性は2倍に向上しています。 最小限の労力で、 各コンポーネント間のマイクロタブを壊して個片化し、 次の製造段階に備えることができる。
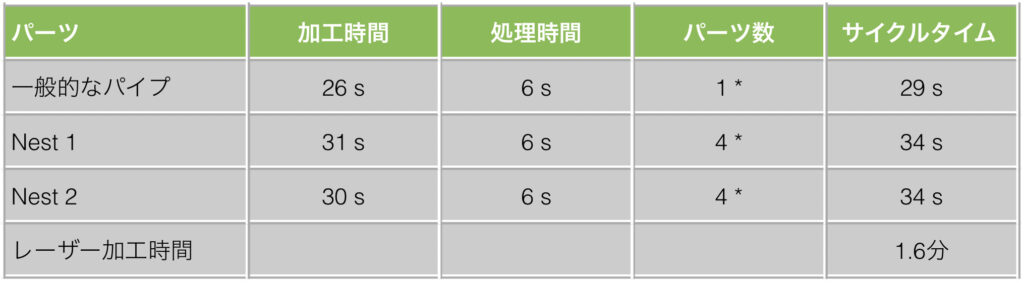
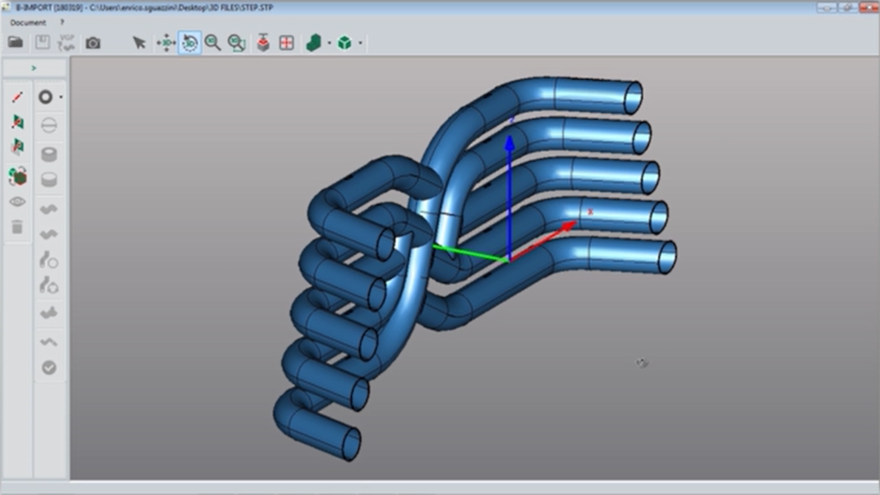
つまり、 マテリアルハンドリングとフィクスチャリングに必要な時間を除けば、 全体の処理時間は7.4分から3分強に短縮されることになります。 たとえ新しい装置の機械加工賃がもっと高くても、 時間と労力が節約されれば、 アセンブリ1個あたりのコストはもっと低くなるのです。
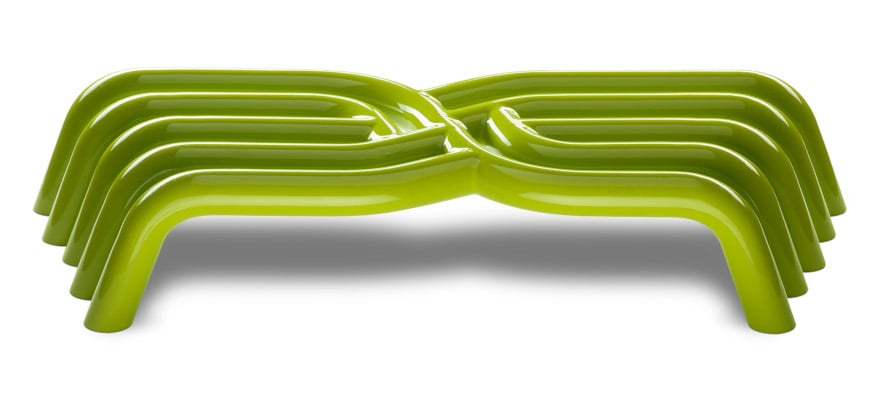
複雑な パイプアセンブリ の製造に最適な方法を決定する際には、 全体像と全体的な影響がどうなるかを検討します。
時間当たりの加工費が低い旧式の機械は、 短期的にはコスト削減を達成できるかもしれませんが、 長期的には製造コストの総額が高くなることが予想されます。
機械、 CNC制御、 オフラインCAD/CAMソフトウェア機能の進歩により、 メーカーはより優れたプロセス制御、 生産性、 材料利用率を実現し、 ひいては収益性を高めることができるようになりました。
パイプ加工機選定ナビを運営するBLM Group Japanでは、実機見学やテストカットサービスを行っていますのでお気軽にお問い合わせください。