3D金属 レーザー加工 はあなたのニーズに最適な選択?
金属切削工程を最適化するために、 新しい機械を導入することを検討されていますか? もし答えが 「はい」 なら、 きっと レーザー加工 のような様々な技術を検討し、 それぞれの長所と短所を理解したことでしょう。
金属切断には多くのソリューションがあり、 その完全な概要を知りたい場合は、 「3D金属切削: 生産工場に適した技術の選び方」 と題した記事をお読みください。
この記事では、 最も近代的で技術的に進んだソリューションの1つである3Dレーザー切断に焦点を当てます。
目次
レーザー加工 は常にベストな選択なのか?
場合によっては最適になります。 このようなシステムは大きな投資であり、 中長期的に大きな利益をもたらすかどうかをきちんと検討しなければならないので、 その価値があるかどうかを理解する必要があります。
次の表は、 Go-To-Marketの分析結果の一部です。 2017年4月から5月にかけて、 総サンプル数397台 (BLMグループのレーザー顧客/競合ブランドのレーザー顧客/レーザー以外のユーザー) に対して実施した 「価値提案における効果向上」 です。 簡単にお分かりのように、 レーザー導入を阻む要因は多く存在します。
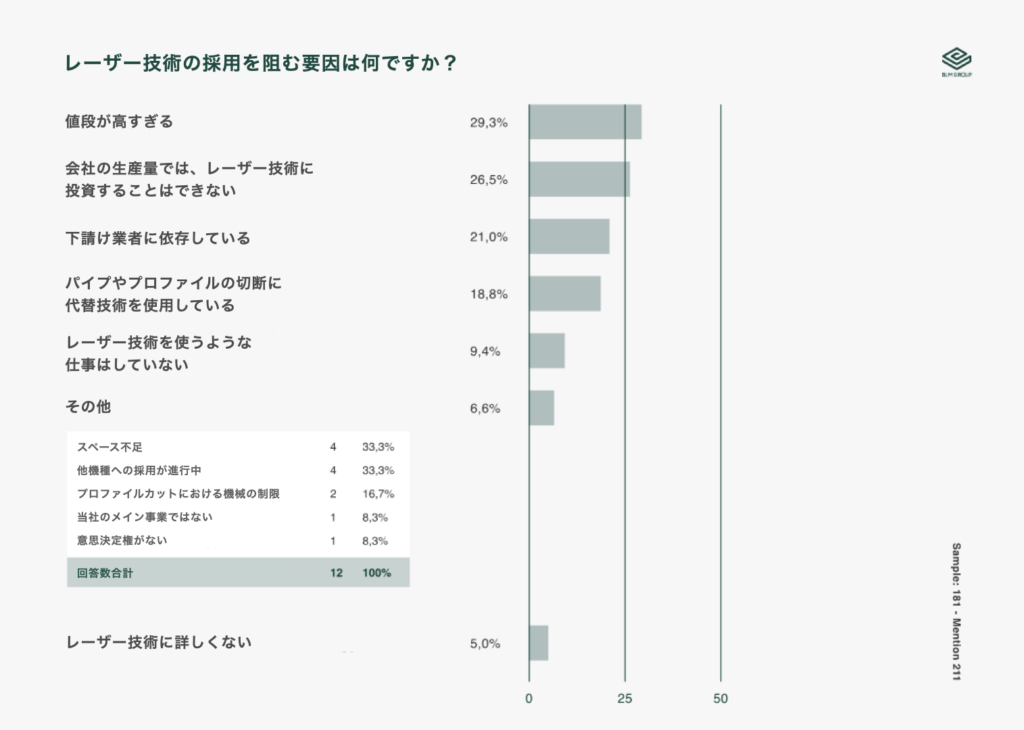
3Dレーザー加工に投資することで、 本当は効果の出るいくつかの事例を紹介します。
– レーザーシステムが多くの機械加工を代替し、 部品あたりの時間とコストを削減する場合
– 何よりもまず柔軟な技術が必要な場合
– 切断品質が非常に重要な場合
– 自動車、 航空宇宙、 家具、 デザインなど、 3Dレーザー切断が特に適している特定の産業や工程に適している場合
レーザー加工 技術で部品単価を劇的に下げるには?
複数の機械加工を置き換えることで、 部品当たりのコストを削減することができます。 レーザー技術を使って金属を切断すると、 部品1個あたりのコストを50~90%削減できると言われています。
これは大きな節約であり、 この技術の利点が主な理由です。
→ 複雑な形状の加工が可能で、 コスト増がほとんどない。
→ 高い生産性と柔軟性
→ 他の部品との接続を可能にする接合部の作成と溶接の簡素化
→ 大量生産のコストでプロトタイプや生産前部品を製作できます。
→ 少ない人員: レーザー加工は、 従来の技術に比べ、 平均で5人少ない人員で行えます。
→ 機械の小型化:従来の加工方法と比較して、 20%から30%のスペース削減が可能
→ 100分の1ミリに近い加工精度で、 無駄を省き、 その後の仕上げ作業も削減できます。
技術の柔軟性
レーザー技術は、 工具の交換が不要で、 さまざまな材料の切断に適しているため、 柔軟性があることが特徴です。 具体的なメリットを得るためには、 シンプルで汎用性の高いプログラミングソフトウェアを搭載したハイエンドマシンを選択する必要があります。
フレキシブルな5軸レーザー切断システムに求められる機能をご紹介します。
プログラミングソフトウェア
新しいオペレーションを素早くプログラムするために、 ソフトウェアは以下の機能を備えている必要があります:
→ オフラインで新しい生産バッチをプログラムし、 マシンが別のジョブを処理している間に、 そのまま生産に移行できること。
→ 他社製 CAD ソフトウェアから 3D ファイルをインポートできること。
→ 切削経路をすばやく特定すること。
→ 潜在的なクリティカルポイントを特定・解決し、作業サイクルを簡単かつ直感的に改善すること。
→ 作業サイクルをシミュレーションし、完全に安全な状態で生産を開始することができること。
切断パラメータの自動最適化
柔軟性の高いレーザー切断システムは、 切断速度、厚み、 切断する材料の種類、 ヘッドの傾きなど、 さまざまな要因に基づいて切断パラメータを自動的に最適化します。
冶具・マテハンシステム
高価な治具の使用や、 搬出入作業を回避することができます。
切断の品質、 自由度、 スピードは、 レーザー加工 が差をつけるところ
5軸レーザー切断システムは、 補間された5軸CNCシステムに搭載されたレーザー切断ヘッドで構成されています。
フライス加工や旋盤加工で一般的に使用されている5軸ソリューションが、 レーザーと統合されることにより、 生産性と柔軟性の新しい基準を設定する技術となります。
切削速度
レーザーは、 変形や破損のない非常に高速で正確な切断を可能にします。
自由自在なヘッド動作
ヘッドの5軸モーションにより、 曲がったパイプ、 ハイドロフォームチューブ、プレスシート、 引き抜きパイプなどの3次元プロファイルに複雑な形状の切断を行うことができます。 また、 カッティングヘッドを傾けることで、 フライス盤では不可能な狭い面への加工も可能です。
多彩な素材
ステンレス、 鉄、 銅、 真鍮、 アルミニウム、 チタン合金など、 さまざまな素材を切断することができます。 従来の切断方法とは異なり、 切断する材料に応じて工具を変える必要がなく、 レーザービームだけが 「工具」 として必要です。
複数の加工を1つに統合
ドリル加工、 フライス加工、 バリ取り: レーザー切断のおかげで、 さまざまな切り屑の除去作業を、 高速で再現性の高い1つの作業に置き換えることができます。
薄い材料
レーザーは、 プラズマや酸素ガス切断などの切粉除去システムや他のタイプでは加工が困難な、 非常に薄い材料でさらに有利に働きます。 レーザー切断では、 切断経路付近のすべての熱影響が排除され、 ブランキングやパンチングなどの機械的切断方法に特有の機械的変形も排除されます。
切断パラメータの自動最適化
研究開発への継続的な投資の結果、 フォーカス位置の管理、 ガス圧の調整、 その他多くのパラメーターを自動的に最適化し、 最高の切断品質と使いやすさを常に保証するシステムが市場に出ています。
レーザー加工 、 多くの産業で卓越したソリューション
この技術に急速にシフトしている産業があります。
自動車関連
3Dレーザーカットは、 多種多様なパーツの製造に最適なソリューションです。
→ ハイドロフォーム (アーム、サスペンション、メカニカルサポート)
→ スタンプシート (車体内部部品、荷物棚、ドア)
→ 曲面パイプ (排気システム、シャーシ、サポートバー)
この分野では、 レーザーシステムを使用すると、 次のことが可能になります。
→ 極めて薄く軽量なさまざまな部品を、 形状や表面状態を変えることなく高速で切断します。
→ 切断プロファイルの品質を維持しながら、高精度な切断を行います。
→ 非常に複雑な三次元形状の切断
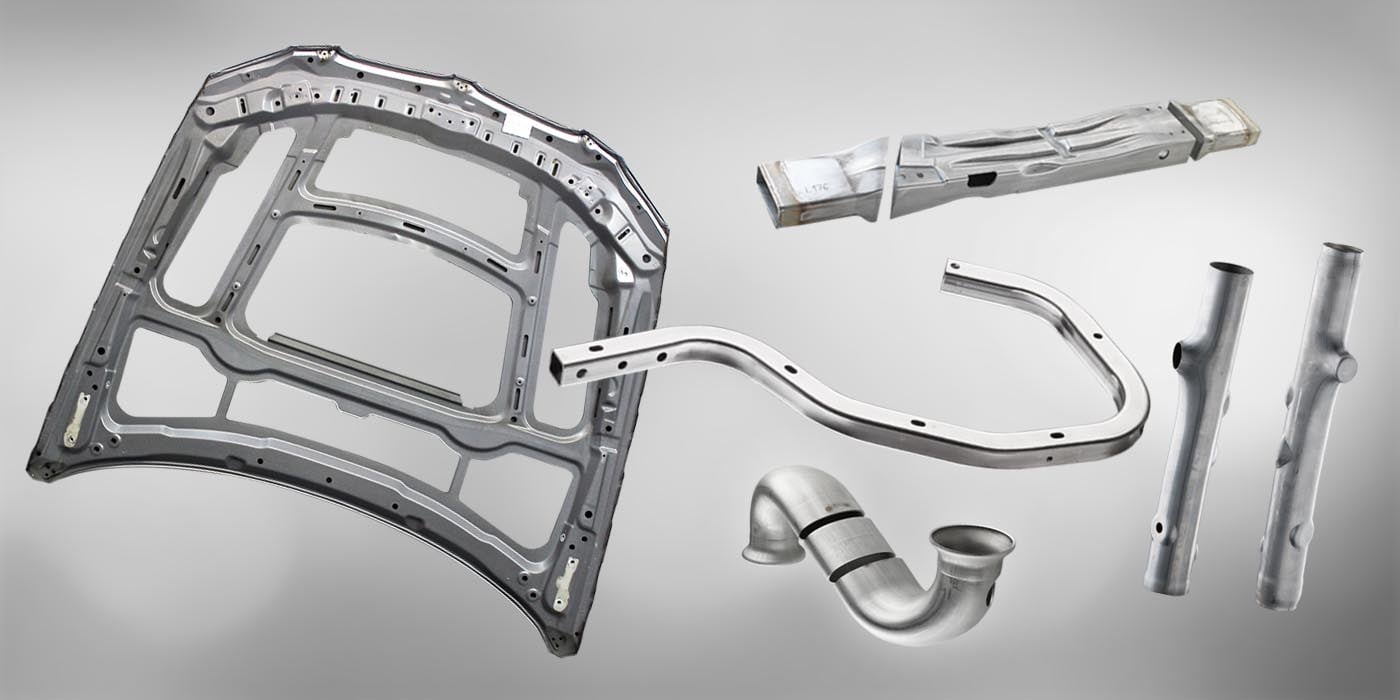
航空宇宙
この分野は、 精度や品質の面で常に最高の品質基準を持ち、 チタンやアルミニウム合金などの軽量で耐性のある素材を使用することを特徴としています。
特殊な形状の部品を製造する場合、 レーザーを使用することで以下のような利点が得られます。
→ 切断や切り屑の除去とは異なり、 非接触で加工できるため、 変形や微小破壊を防ぐことができます。
→ 熱影響部がなく、 正確で高速な切断が可能です。
→ 工作機械につきものの切削液や切り屑が出ません。
→ 複数の加工を1つにまとめることが可能で、 半製品の取り扱いが軽減されます。
→ チタンやアルミ合金の切断が可能です。
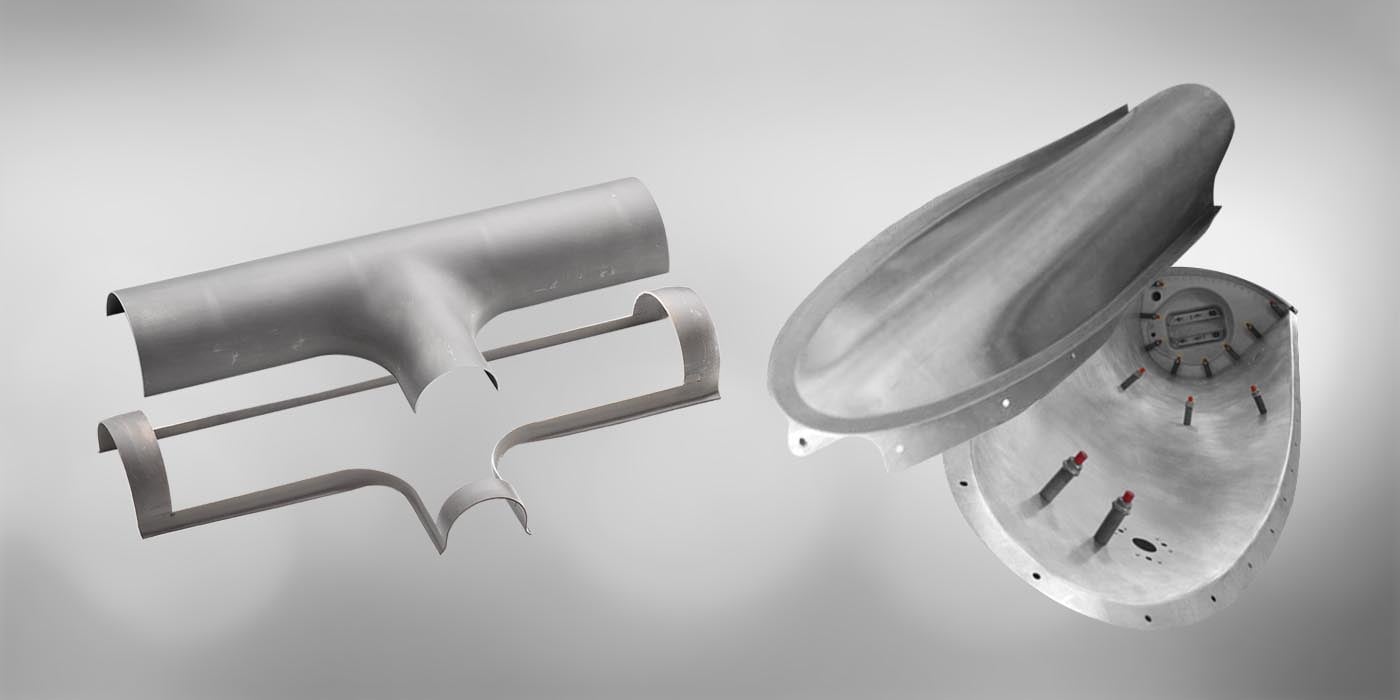
家具 ・ デザイン
レーザーは、 非常に複雑な3次元形状や優れた仕上げの部品を得るために必要なエネルギー消費と工程数を削減し、 デザイナーがトレードオフなしで思い描いた形状を実現する機会を与えてくれます。
レーザーは、 まるで極細のペンを使っているようなものです。 そのため、 優秀なデザイナーは自由に創造性を発揮することができるのです。