パイプレーザー の新たな競争力 (LT14 & LT24)
イノベーションを起こすことは、 単に利益率を上げるための創意工夫ではありません。 なぜなら、 世界は変化しており、 それに伴って顧客のニーズやそれを満たすための技術的なソリューションも変化しているからです。 構造的な観点から見ると、 パイプレーザー はこの技術的な変化に不可欠な要素であり、 多くの企業のイノベーションプロセスに積極的に貢献し、 大きな利益をもたらしています。
– 構造物のパイプや梁の継ぎ目や節を、 従来技術では不可能な精度と生産性で作ることができます。
– 全モーター化により、 環境負荷の低減に貢献します。 パイプレーザーシステムは、 金属リサイクルから物流、 現場での組み立てまで、 鉄骨建築のあらゆる利点を最大限に活用することができ、 全体のランニングコストの削減に貢献し、 従来のプロセスと比較してエネルギー効率の高い技術です。
– また、 作業者の労働環境を改善し、 製造する部品の技術レベルを向上させることで、 プロフェッショナリズムとプレステージのイメージを生み出すことができます。
目次
新規受注の獲得:第一の重要な目標
すでに、 上記のような利点は、 新しい注文を獲得し、 利益を生み出す能力を高めることができます。 しかし、 これらのシステムの本質的な特質が、 日常業務にプラスの影響を与えることについても、 少し述べておく価値があると思います。
迅速かつ正確な見積もり提供能力
すべてのパイプレーザーシステムは、 Artube CAD ・ CAMプログラミングソフトウェアを使用しており、 作業サイクル全体をシミュレートし、 各パーツの生産時間を迅速かつ正確に算出することができます。 さらに、 Protubeモジュールを使用することで、 生産指示の管理やERPシステムとの連携も可能です。
迅速かつ最低コストで製造する能力
LT14とLT24、 そしてその他全てのBLMグループパイプレーザーシステムが持つ、 汎用性、 精度、 生産性が鍵です。 これらは実用的な利点です。
– 実現可能な部品点数が増加する。
– 製造される部品の精度と品質が向上する。
– 生産ロットが小さく、 変化が激しい場合でも生産性が高い。
使いやすく、プログラムしやすいシステムに依存する能力
LT14とLT24では、 シンプルでユーザーフレンドリーなプログラミング、 完全自動の材料処理と機械のセットアップ、 この種の技術に経験のないオペレーターでも簡単にシステムを操作できることに信頼を置くことができます。
これらの点は、 一方ではコストと生産時間を削減し、 他方では精度と製造部品の品質を大幅に向上させ、 ユーザーの利益率を大幅に増加させることができます。
大口径用 パイプレーザー 機
LT14
LT14は、最小25mmから最大355mmまでの直径、最大18mまでの長さのプロファイルや管状部品を、最大100kg/mの重量で3Dレーザー切断する全自動パイプレーザーシステムです。
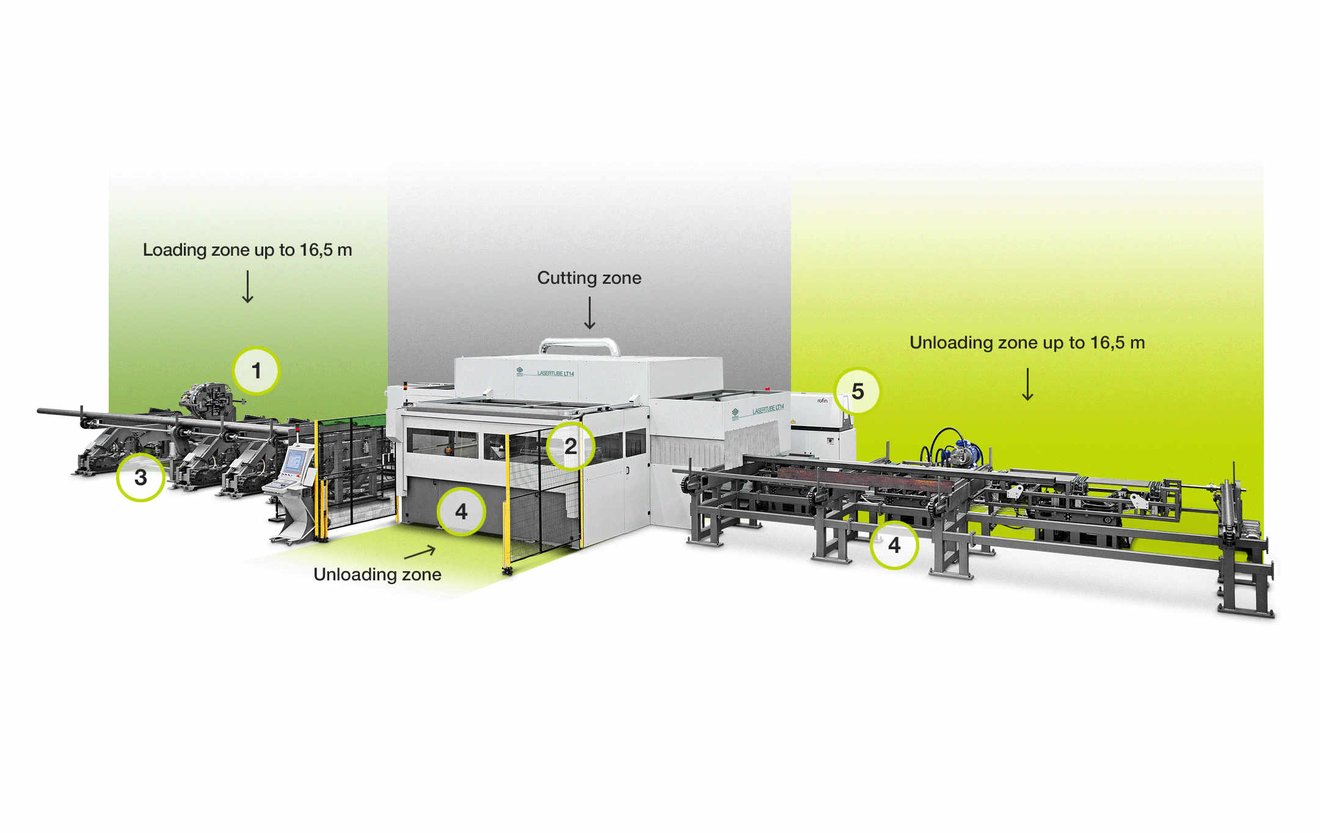
LT24
LT24は、 最小直径80mmから最大直径610mm、 最大長さ18mまでのプロファイルやチューブ状部品を、 最大重量300kg/mで3Dレーザー切断する全自動パイプレーザーシステムです。
大型パイプやプロファイル用のパイプレーザーシステムLT14とLT24は、 建設業界などで起きているイノベーションのプロセスに寄り添い、 まだ多くの人が持っていないツールや機能を使って競争力を発揮できるよう設計されています。
丸パイプ、 角パイプ、 鉄、 軟鋼、 合金鋼、 ステンレスなどのオープンセクションを加工することができ、 新しい作業のたびに交換しなければならない特別で高価な設備は必要ありません。
LT14 & LT24 パイプレーザー 切断システムの主要コンポーネント
3D パイプレーザー カッティングヘッド
5つのCNC軸を持つ3Dレーザー切断ヘッドは、 パイプの表面に対して直交または傾斜して加工することができます。 つまり、 直交切断、 傾斜切断、 面取り、 半面取りなどが可能で、 管や形状のあらゆるタイプのかみ合わせを作ることができます。
この技術は、 後の溶接作業も容易にする。 レーザーは高い幾何学的精度で切断を行うため、 後で表面研磨を行う必要はありません。
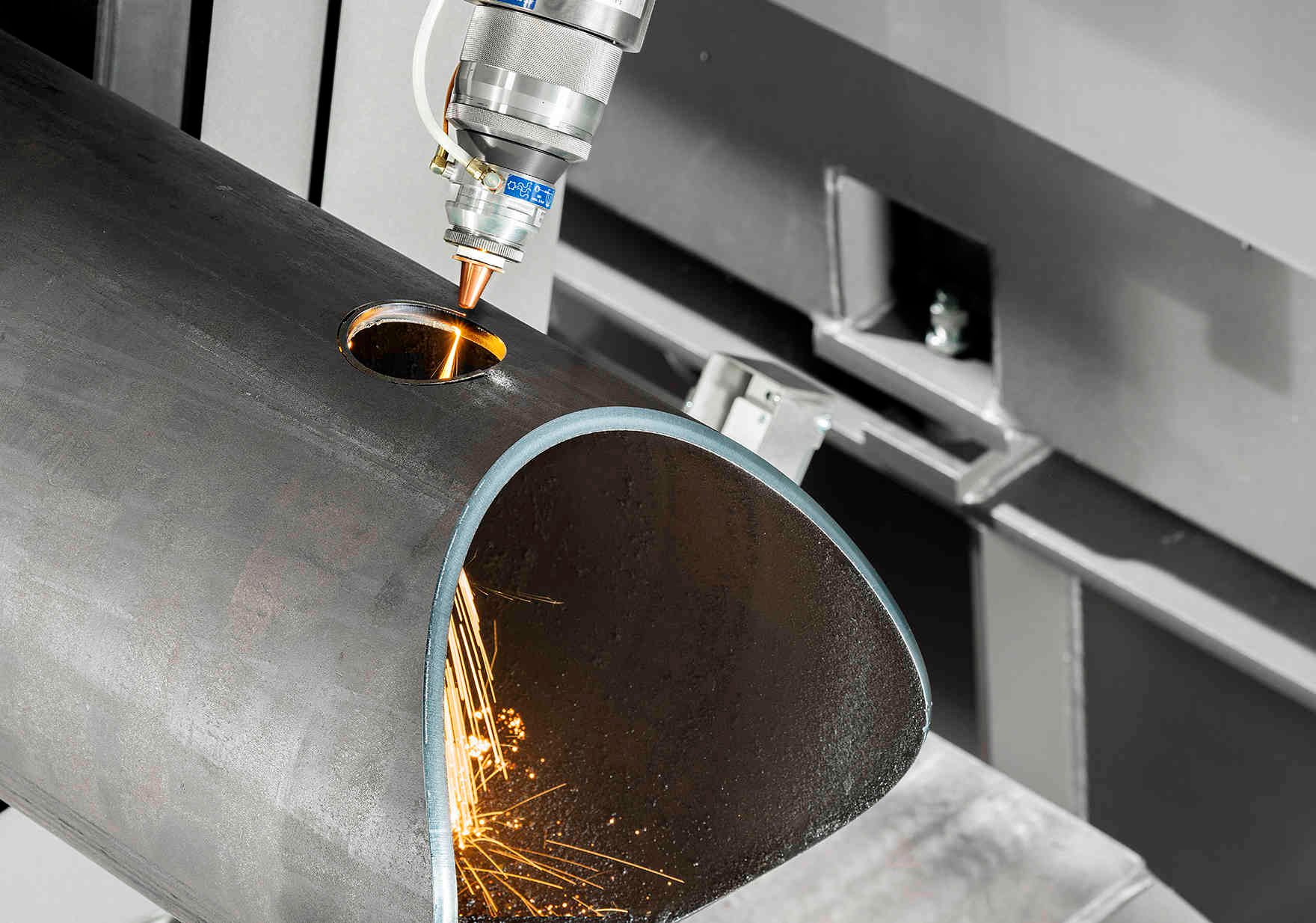
スピンドル
LT14、 LT24システムの精度向上に大きく貢献するのが、 自動セットアップ機能を備えた3本の全電動スピンドルによるワークハンドリング機能で、 軽量パイプは潰れにくく、 重量パイプはしっかりとホールドできるよう設計されています。
切断作業中のスピンドルの位置は、 バーの動きを最小限に抑えるために自動的に管理されます。 2本のスピンドルは、 パイプをスライドさせる機能とクランプする機能の2つを兼ね備えています。 こうすることで、 バーが完全にフリーになることはなく、 より正確なカットが可能になります。
カッティングヘッドは、 スピンドルの片側からもう片側に自動的に切り替わり、 3つの異なる位置でパイプを切断することができます。
ヘッドカット : スピンドルの下流側で、 バーの最終部分を切断します。
センターカット : 2本のスピンドルに挟まれた中央部分を切断します。
テールカット : 貫通スピンドルの上流側で、 棒材の初期部分を加工するヘッド。
このように、 カッティングヘッドは、 スクラップを発生させることなく、 またスピンドルがパーツを再加工する必要もなく、 パイプの全長にわたって加工することができます。
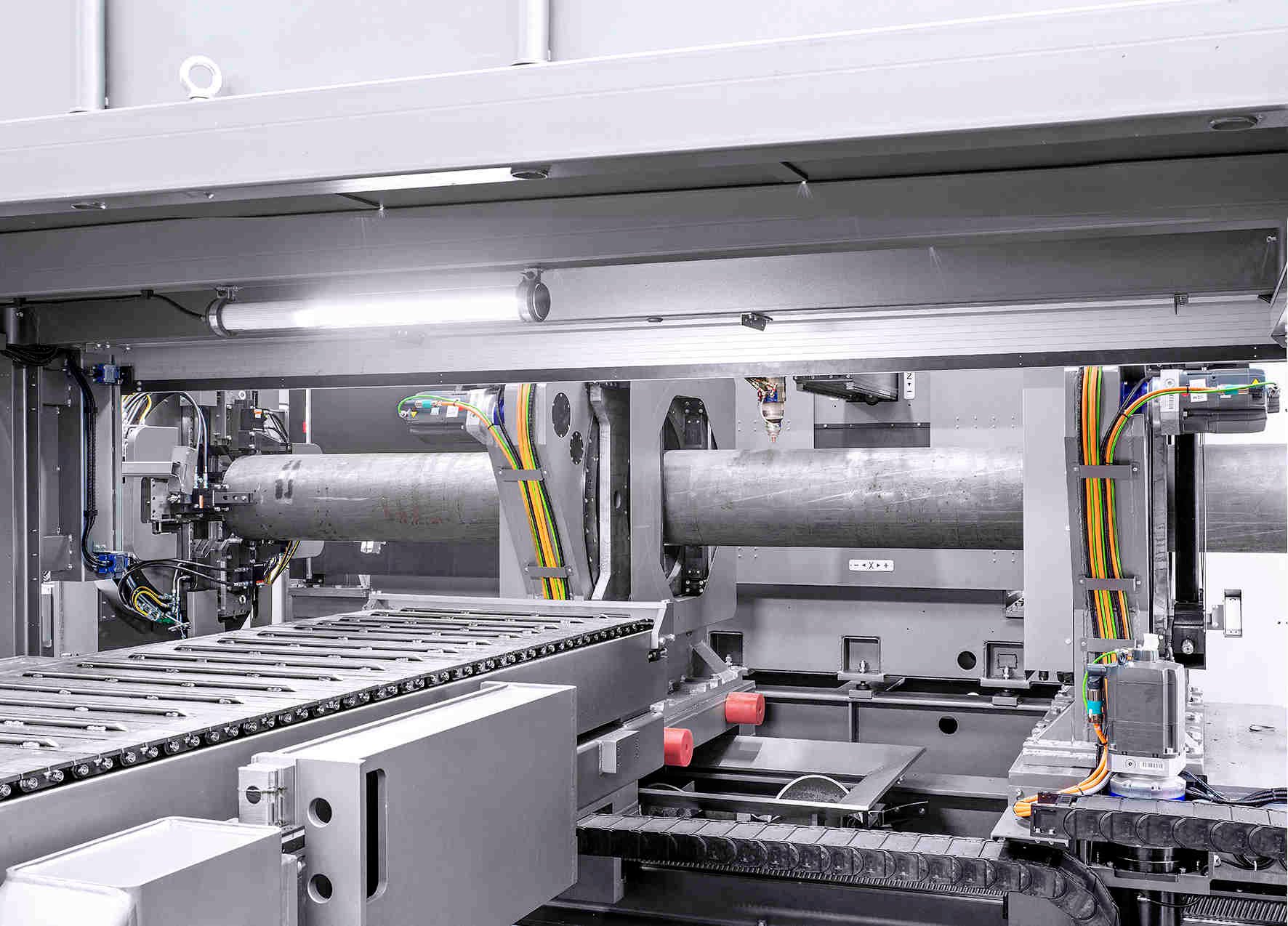
Active ツール
生産性、 安全性、 品質、 自動化、 使いやすさを保証するために作られたActive ツールは、 オペレーターの実務経験に関係なく、 より短時間で最高の結果を得るための最先端の技術的ソリューションです。 LT14とLT24には、 以下のActive ツールスを装着することができます。
アクティブピアス
中厚物部品の生産性を向上させるため、 材料の突き抜けを検知し、 レーザー切断時のドリフトを防止するプロセスコントロールとして機能します。
アクティブフォーカス
材料や厚みに応じてフォーカスを自動調整し、 切断品質を向上させる機能です。
アクティブメール
メンテナンス管理をサポートする機能です。 実行すべき作業に関する情報を提供し、 メンテナンスレポートを含む電子メールを送信します。
レニショー
加工作業のセンタリングを行うために、 カッティングヘッドに直接設置された測定システムです。
タップ & ドリル
このユニットには、 自動ツールストアとツールの整合性を監視する機能があります。 また、 フロードリル装置を使用して、 M3からM16までのネジ穴を順番に開け、 タップすることができます。
長年の技術開発により、 LT14、 LT24、 その他全てのBLMグループのパイプレーザーシステムは、 性能の劣るシステムとは一線を画すものとなっています。
パイプレーザー プログラミングソフト
LT14とLT24は、 完成品を作るために必要な多くの機械加工作業 (一部は手作業) を代替することができますが、 搭載されているCAD / CAMプログラミングソフトウェアArtubeは、 CADからCAMマシンプログラミング環境までの作業工程全体のプログラミングを簡素化することが可能です。
長年かけて開発されたArtubeは、 パイプレーザー加工機のプログラミング用ソフトウェアとして市場で最も先進的なものです。 Artubeは、 様々な分野での作業を簡素化し、 強化するための様々な機能と追加ソフトウェアパッケージを提供しています。
CAD/CAMソフトウェアであるArtubeは、 パーツプログラムを作成し (CAM) 、単一のパーツやフレーム、 複雑な構造も一から作成することができます (CAD) 。さらに、 チューブ間のジョイントは、 サポートとジョイントの幅広いライブラリを使用して自動的に作成されます。
Artube 3D CAD環境でパーツをインポートまたはモデリングすると、 最適なツールパスを自動的に作成し、 傾斜切削のためのヘッドの正しい傾斜を正確に定義し、 パス全体にわたって切削のための最適なパラメータを適用します。
すべての操作は、 レーザー切断パスの3Dグラフィックでグラフィカルに表現され、 明確に色分けされます。 このような表現により、 部品がどのように加工されるかを理解し、 生産の安全性とプログラミングの迅速性を高め、 正確に、 簡単に、 即座に加工することが可能になります。
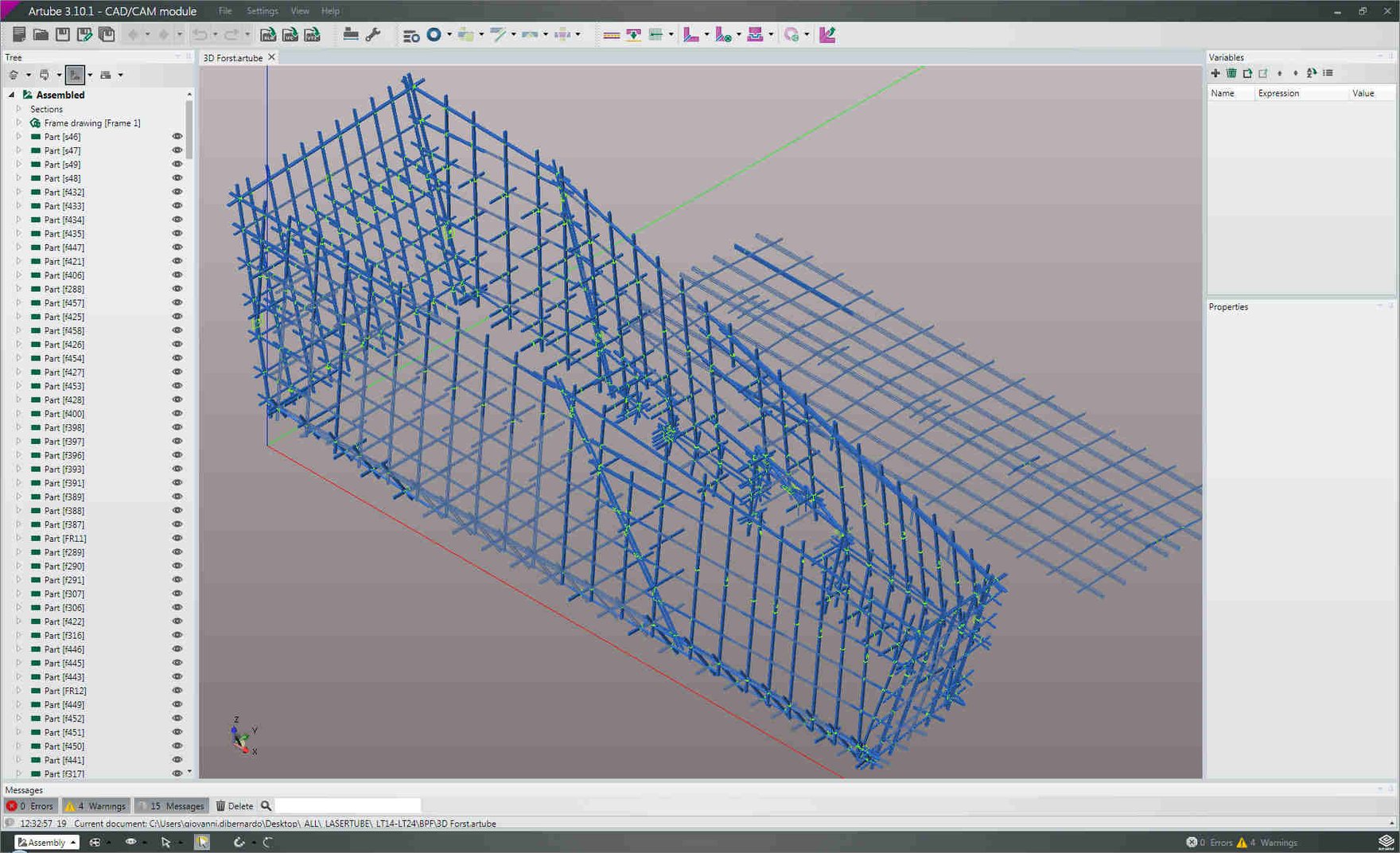
構造分野では、 ArtubeはIGES、 STEP、 IFC (Tecla) ファイルを読み込むことができ、 構造物の全要素をオペレーターがすぐに利用できるようにします。 その結果、 各要素を抽出し、 必要に応じて修正し、 加工可能なマシンプログラムに変換することができます。
これにより、 従来のIFCファイルからSTEP、 IGES、 X_Tへの変換に必要だった時間がすべて相殺され、 コストと柔軟性の面でかなりの優位性を持って設計とプログラミングの時間を短縮することができるのです。
自動搬入出
LT14とLT24は、 システムへ搬入 ・ 搬出するハンドリングフローを迅速かつ安全に処理するための特別な完全自動ローディングとアンローディングシステムを備えています。
完成した部品は、 切断工程を中断することなく、 連続的にアンロードされます。アンローダーは
– 切断室内のコンベアベルトを使用して、 長さ3.2mまでの短いパーツを取り出します。
– 長い部品は、 切断筐体の下流にあるアンローディングチェーンを使用して取り出します。
チェーンローディング装置はコンパクトで、 さまざまな形状やサイズのパイプや形材に対応し、 調整や追加設備は不要です。 異なる断面やサイズの部品は、 ローダー上で強制的な位置決めをすることなく、 順番に並べることが可能です。 各バーは、 人手を介さずに分離 ・ 積載され、 その後、 機械が部品をピックし、 適切に処理されます。 このように、 生産エリアへのマテリアルハンドリングの流れを変更する必要はなく、 さらなる投資も必要ありません。