建築構造における レーザー切断 の利点
レーザー切断 の精度と技術的特徴は、 構造用途の溶接継手の生産に新しい展望を開き、 複雑な形状の接続部を従来よりも高い精度と速度で作成することを可能にしています。
製造業者は、 梁や管をフレームや構造物などの複雑な製品に加工する際に、 日々さまざまな技術的および規制的要件に取り組むよう求められている。
大口径のパイプや梁に可能な加工は主に
パイプの端部加工: 一般的には、 サイズに合わせた切断、 さまざまなタイプの継手や金具を挿入するためのノッチ加工、 組み立てや溶接作業を容易にするための面取りや歯形加工で構成されます。
中央部の加工: 通常、 軽量化カット、 パイプ通過用のノッチ、 他の梁、 パイプ、 部品と交差するための様々な形状から構成されます。
建築分野では、 接合部の加工が特に重要です。 梁やパイプをつなぐ基本的な接合部は、 鉄骨建築において常に開発され続けています。
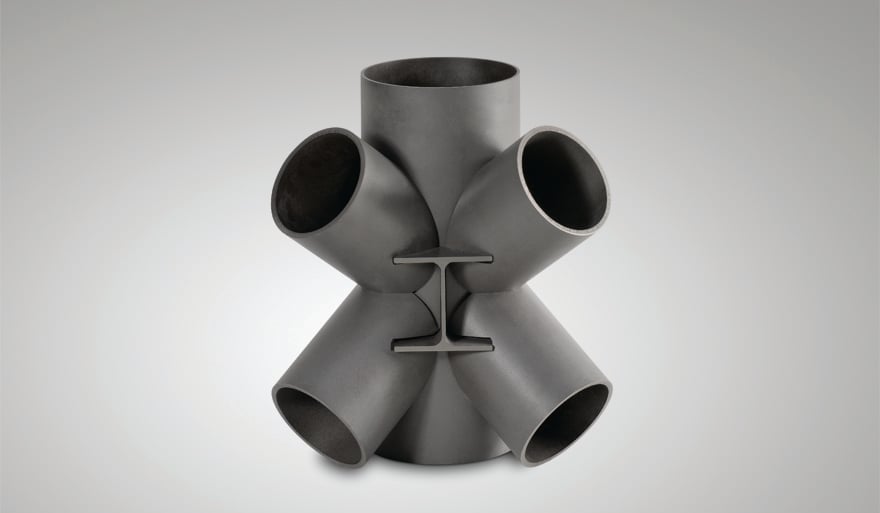
この分野でのレーザー切断の主な利点は以下の通りである。
材料の節約と組み立ての容易さ
レーザー切断の精度と汎用性により、 最も多様なパイプとプロファイルのインターロックソリューションを作成し、 機械的強度を向上させるだけでなく、 組み立ての複雑さを軽減し、 時間を短縮することができます。
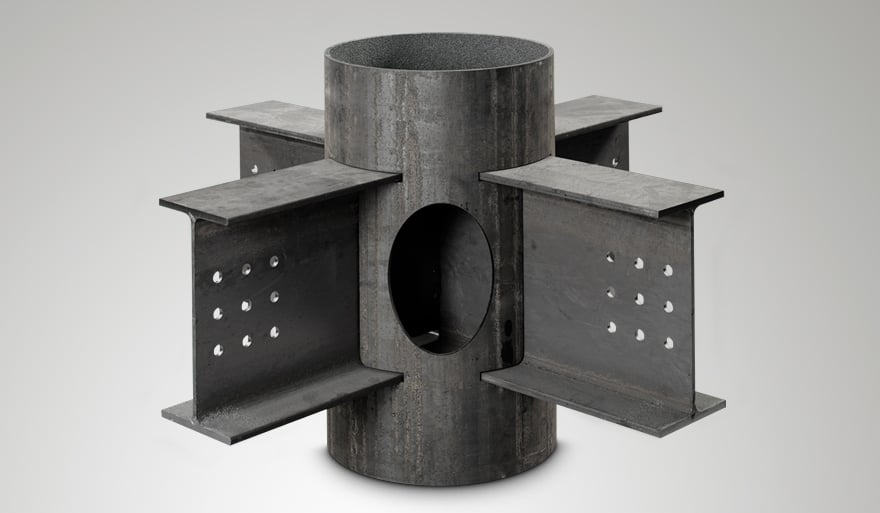
その実例が、 上の写真のジョイントです。 ボルトやリベットなどの締結部材を使用せず、 材料重量を63%、 製造コストを62%削減することができた。
次の写真は、 板とボルトで製作した同種のジョイント (写真A) と、 レーザー切断装置LT24で製作したジョイントの各構成要素 (写真B、 C、 D) を比較したものである。
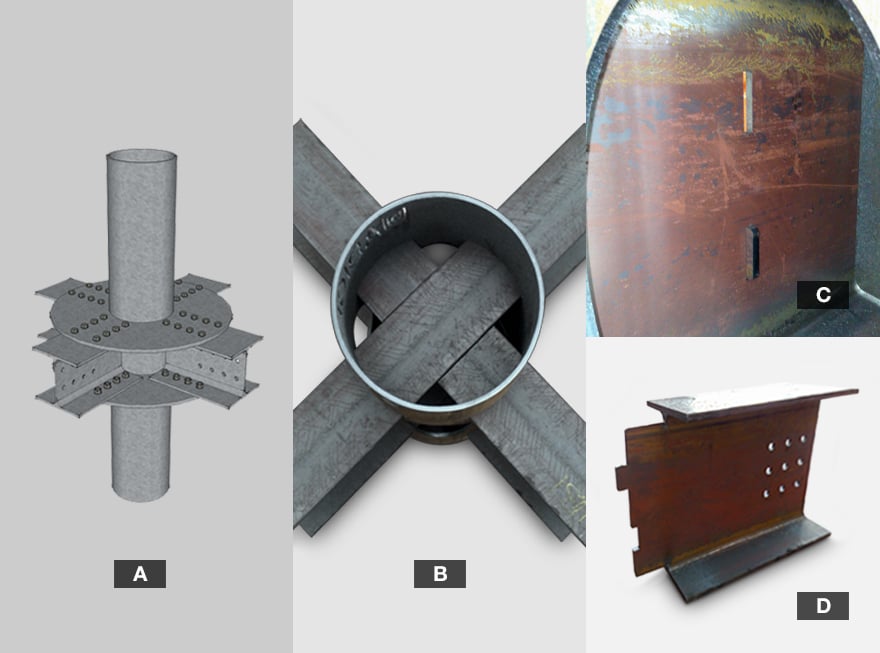
接合部を通過するIPEビームへの加工(C) | 他の2本のIPEビームへのパイプ端の加工(D)。
精度・品質
3Dレーザー加工機を使用することで、 プラズマや酸素を使用した切断技術よりも精度の高い加工が可能になります。
また、 熱影響部* が極めて小さく、 バリがない滑らかな切断面が得られます。
これにより、 製品の研削加工が不要になり、 構造体のさまざまな部品を組み立てたり溶接したりする準備が整うため、 時間とエネルギーを節約することができます。
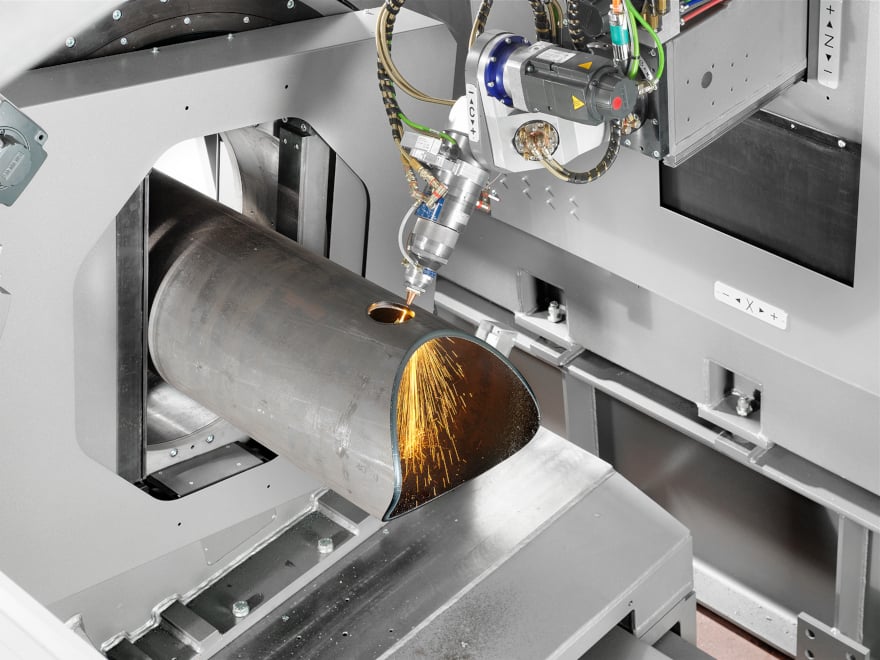
熱影響部を減らすということは、 温度変化により化学的 ・ 機械的特性が変化する可能性のある材料の部分を減らすということです。
さらに、 最先端のレーザー切断システムには、 切断パラメータを自動的に最適化する機能が備わっています。 これは、 生産性やプロセスの堅牢性を高めるだけでなく、 オペレーターの経験に関係なく、 最高の切断品質を実現するものです。
*熱影響部
熱影響部とは、 熱切断加工 (材料の溶融や局所的な昇華を利用して金属を切断する加工) において発生する高熱によって、 化学的 ・ 機械的特性が変化した鋼材の部分である。
鋼の場合、 この急激な温度変化によって局所的な硬化が起こり、 材料が硬くなると同時にもろくなる。また、酸化や窒化などの化学変化を起こすこともある。
レーザーの利点
レーザーは、 プラズマや酸素燃料と異なり、 その技術的特徴と表面の極めて小さな部分にすべてのビームエネルギーを集中させるという事実により、 熱影響部を大幅に減少させることができます。
一工程で溶接可能な部品を作成
被覆アーク溶接は、 現在、 現場で使われている唯一の溶接方法で、 溶加材の溶け込み具合によって次のような特徴がある。
– 完全溶け込み溶接
– 部分溶込み溶接
– コーナーシーム溶接
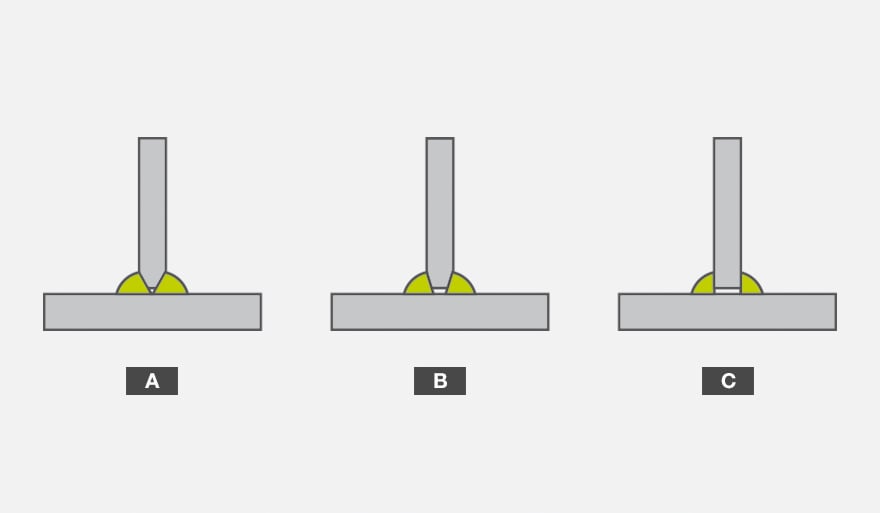
完全な継ぎ目の溶け込み溶接は、 材料の連続性をどこにも妨げないため、 最高の性能を発揮する。 従来の生産システムで実施する場合、 溶接する端部を手作業で正確に準備するために、 熟練したオペレーターが必要となるため、 最もコストがかかる方法でもあります。 確立された規制の枠組みに従った端部の形状は、 角度や面取りの深さ、 ショルダーサイズ、 溶接端部間の相互距離など、 所定の幾何学的仕様を尊重する必要があります。
この点で、 3Dレーザー切断システムの使用は特に有利です。 なぜなら、 部品は1回のレーザー切断工程で作られ、 仕様通りに切断され、 溶接の準備が整うからです。
大型パイプやプロファイルの3Dレーザー切断システムでは、 さまざまな傾斜の面取りや、 切断端全体に沿った可変の傾斜が可能である。 これにより、 パイプや形材が互いに直交していない場合でも、 面取り角度を規制の枠組みで設定されたパラメーター内に収めることができるようになります。
さらに、 大型の管や断面用の3Dレーザー切断システムで作ることができる多様な幾何学的形状により、 接合部の強化に使用できる歯を含めることができ、 接合する端部間の距離を維持して溶接工程を簡略化することができる。
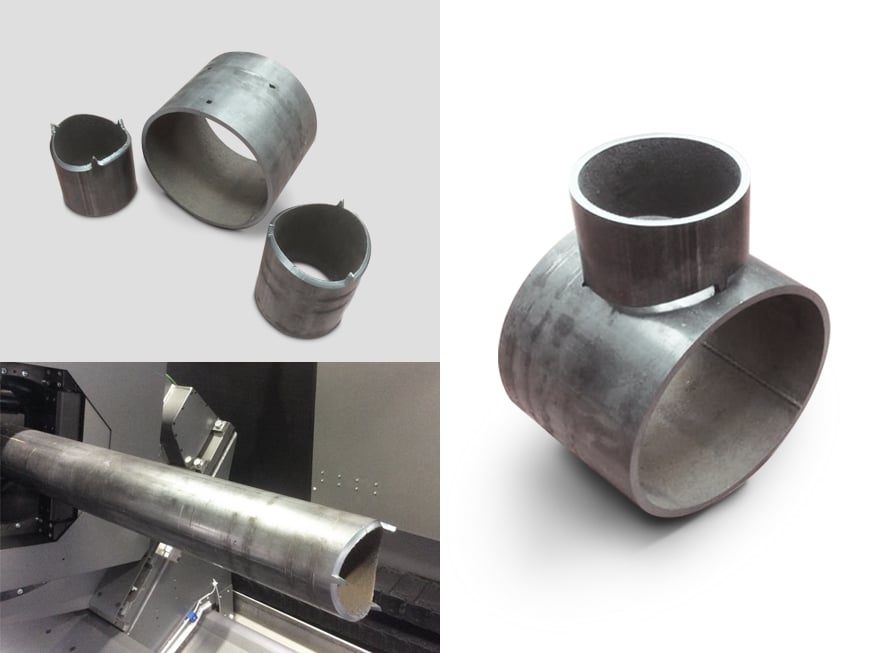
これらのシステムの中には、 高度なCAD/CAMソフトウェアツールがあり、 ジョイント形状、 およびあらゆるプロジェクトの作成を加速させる一連の機能を備えたライブラリをユーザーに提供します。
3Dレーザー切断システムを使用することで、 2次的な組み立て段階がよりシンプルになり、 経験の浅いオペレーターでも最適な結果を出すために溶接することができます。
大型パイプやセクションの3Dレーザー切断システムは、 その多くの利点から、 構造用途だけでなく、 農業 ・ 産業車両製造、 造船、 石油 ・ ガス、 石油掘削装置建設、 発電所にも使用することができます。
このシステムは、 さまざまな用途において、 品質、 柔軟性、 生産性の新たな基準を導入することができます。
パイプ加工機選定ナビを運営するBLM Group Japanでは、実機見学やテストカットサービスを行っていますのでお気軽にお問い合わせください。