なぜ、光で金属を切断できるのか? Part 2
レーザーで硬い金属を切断できる理由、そして、レーザー機の歴史とこれからについて、解説しております。
板金アプリケーション
今日では、10kW、さらには12kWの発振器を備えたシートレーザ切断システムを見つけることは珍しくありません。切断できる鋼(または他の金属)の厚さは30~40mm(~1.5インチ)に達することができます(それ以上はレーザー切断の用途が限定され、他の方法が使用されます)。より多くのパワーを持つことで、作業速度が向上し、システムの生産性が向上し、結果として部品あたりのコストが削減されます。 要するに、パワーと達成可能な生産性は、非直線的な進行ではありますが、より大きくなっており、これは技術的な論理ではなく、マーケティングに直接影響しています。
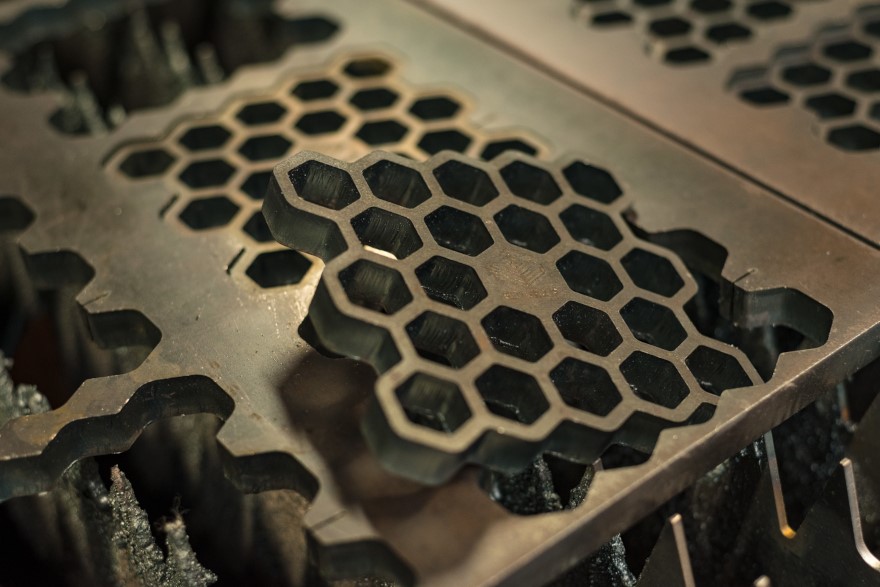
パイプレーザー機とシートレーザー機は、別物
シート切断の用途からパイプ切断の用途に目を向けると、レーザーパイプ切断システムのメーカー間での競争がはるかに少なくなっており、目立ちたいからといって、より多くの記録数を追いかける必要性に悩まされることが少なくなっています。
パイプは「シートではない」という単純だが基本的なことがあります。
シートカットでは、シートの下に受動支持面という空間がありながらも、できるだけ早く金属の厚さに穴を開けることを意識して、光源から供給されるすべてのパワーを(適切に)「発射」することができますが、パイプの場合、問題は確かにより複雑になります。
それは、パイプは立体物ということです。 レーザービームによって切断された材料の下には、まだワークピースの一部である別の材料があります。レーザーソースによって供給される電力は、投与され、発射されたものの、プログラムされたパスに沿って金属の厚さをカットするだけでなく、反対側の材料にも熱影響による悪影響を引き起こす危険性があります。さらに、ワーク全体が加熱され、切断プロセスの特性が変化するため、より高い生産性を達成するためには、出力が増加するにつれて、ますます洗練された技術的なレーザー出力管理ソリューションを使用しなければならないという結果になります。
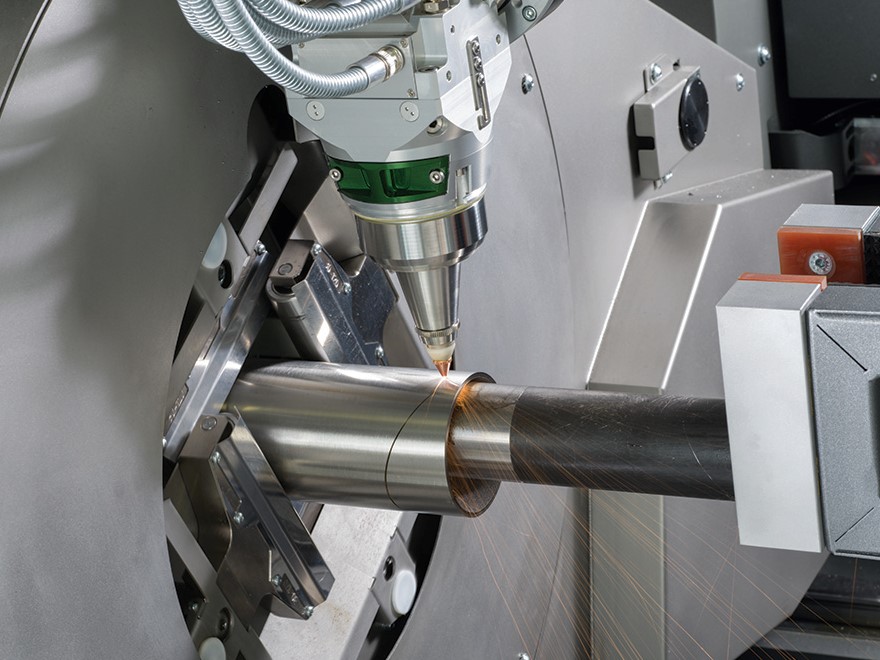
パイプレーザーの発明者
ビーエルエムグループ(特にグループの一部であるアジジェ社)が30年以上前に開発した最初のシステムから、最新のLASERTUBEモデルの開発は驚くべきものでした。
当初は、丸型、角型、四角型のプロファイルのみの切断が可能であったが、生産性に限界があり、満足のいく結果を得るためには、レーザー光源を効果的に管理するための高度な技術力が必要であった。その後、大きな進歩を遂げ、今日では、システム管理の煩雑さとは対照的に、マテリアルハンドリング、レーザ調整が共に全自動化され、生産性は飛躍的に向上しています。
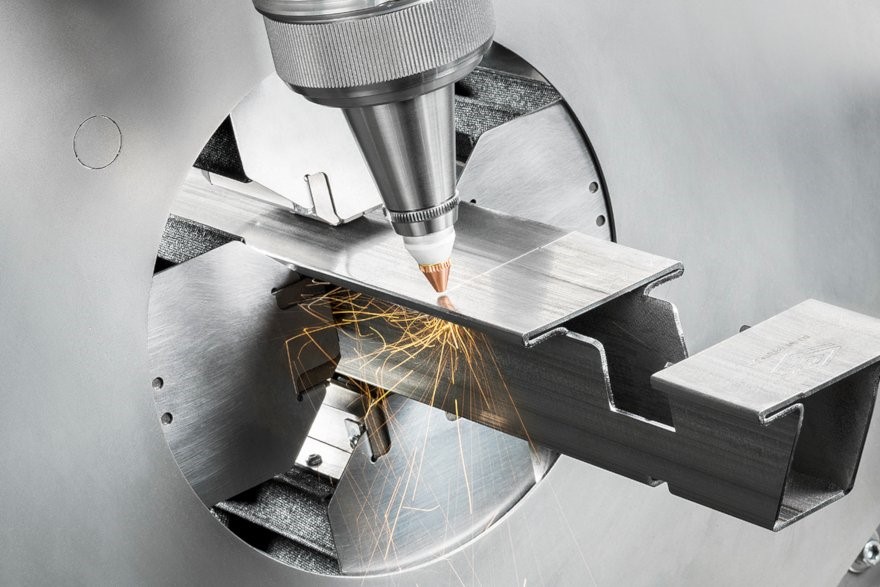
レーザー切断の人気
自動化は生産性を向上させます。 多くの製品で見られるようになってきたカスタマイズの需要に対応するために、生産ロットの数量が小さくなってきています。
そのため、可能な限り短い時間で生産から別の生産に切り替えられることが重要になってきています。
鋼合金、アルミニウム合金、銅や真鍮、材料の厚さやプロファイルの大きなばらつきは、すべてパイプレーザーシステムで簡単に切断することができます。
最も多様な分野での応用範囲が、この技術の成功を証明しています。今日でも、そのアプリケーションの可能性は拡大し続けています。30年以上の歳月を経ても、革新的な技術であると考えられています。
初期投資は依然として重要ですが、達成可能な生産性にエネルギー効率の向上やメンテナンスの軽減などの要素を加えれば、多くの人々がレーザーを受け入れ、一般的に評価されている理由が容易に理解できます。
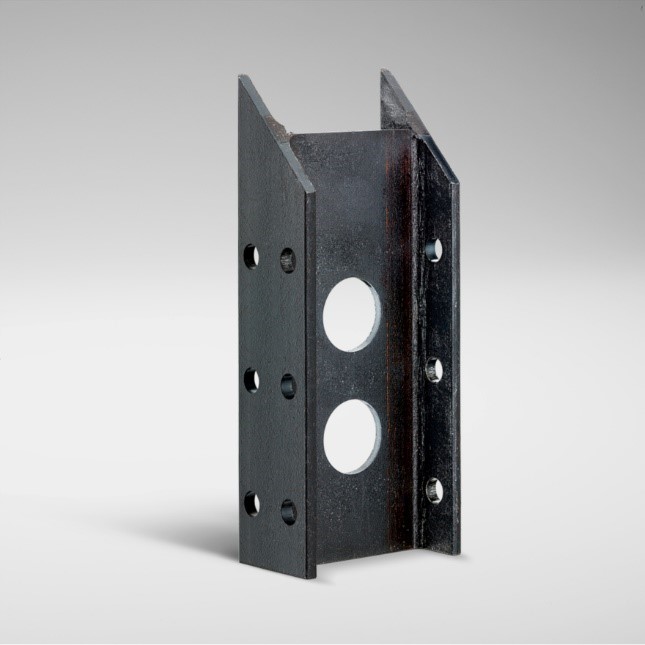
そして今後どうなっていくのか?
では、近い将来何が期待できるのでしょうか?エネルギー効率を改善する余地はまだあるのでしょうか?より低い出力でより厚い材料を切断できるタイプのレーザーを見つけることは可能でしょうか?
傾向としては、レーザー自体の連続的な調整における自動化がますます進み、リアルタイムで切断される材料の特性を測定して考慮に入れるだけでなく、その動作結果を自己評価していくことで、生産コストを削減し、持続的に利益を維持するためにますます必要とされる自動化の最適化と予防保守のロジックを統合します。
これらの分野において、ビーエルエムグループでは短期的に可能な限り最高の技術的ソリューションを提供し、お客様がビジネスを強化し続けるために必要な競争力を確保するために、多くのプロジェクトやコラボレーションを展開しています。
加工品の製作依頼はこちらから!
パイプ加工品製作のことなら
「パイプレーザー加工センター」へお任せください!