パイプレーザー切断機用 自動ストッカーシステム 【7つの利点】
材料搬入出の自動化については、 シートレーザー加工では多くのソリューションが確立され、 複雑化しています。 一方、 パイプレーザー加工機では、 パイプの 自動ストッカーシステム を備え、 材料を自動処理し、 無人で生産変更を行うことができるようになってから、 まだ数年しか経っていない。
ここでは、 パイプレーザー切断機とパイプ 自動ストッカーシステム を組み合わせるメリットについて説明します。
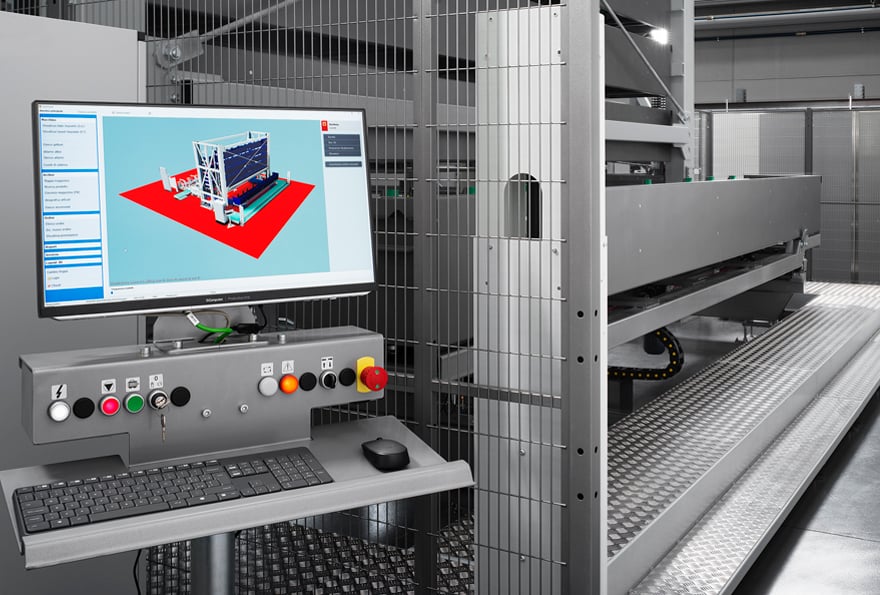
目次
日々の生産性の向上
パイプタワー自動収納システムは、 鋼鉄、 銅、 鉄、 アルミニウムなど、 さまざまな断面や厚さの金属製のパイプが入った多数の木箱が積載される鉄骨構造物です。
加工するバッチに応じて、 切断するパイプは自動的に素早く木箱からマシンローダーに運ばれ、 フォークリフトの運転手や保管システムの管理者などのオペレーターを追加することなく、 パイプのレーザー切断を待つことなく開始することができるようになります。
その結果、 手作業でパイプを処理するよりもはるかに早く、 生産を開始することができるのです。
前のバッチからバーをローダーから取り出すのに必要な時間と、 元の位置に戻すのに必要な時間も考慮すれば、 パイプレーザー切断システムの稼働時間が決定的に増加し、 機械の待機ダウンタイムが減少し、 結果として日々の生産性が明らかに向上するのは明白でしょう。
次のビデオは、 レーザー切断機へのパイプの搬入 ・ 搬出と、 自動収納システムへのパイプの収納を自動で行っている様子です。
LT8.20は、 縦型パイプ収納システムと一体化したパイプレーザーシステムです。 本機の詳細をご覧ください。
仕事の優先順位をすぐに変える
緊急事態や予期せぬ生産ニーズの変化に対応するために、 計画したバッチの順番を変更する (場合によっては、現在のバッチを中止する) 必要が生じることがあります。 自動材料変更ソリューションがあれば、 このような事態にも瞬時に対応することができます。
パイプやセクションバーを一時的に置くスペースを確保する必要がないため、 取り扱いが複雑にならず、 保留中の作業がわからなくなる危険性もありません。
予定されているバッチの順番は、 機械上で直接変更することができ、 また、 あらかじめプログラムされたリストに追加バッチを追加し、 短時間で自動クレート交換を実現することができます。
タワーストレージを使用することで、 生産の切り替えを即座に行うことができます。

工場内のスペースを確保
機械収納システムを解放し、 新しいバッチを開始するために、 前のバッチから残った材料を取り出す必要があることは既に述べたとおりです。
材料は、 邪魔にならないように、 また新しいパイプ束の到着を妨げないように取り除かなければなりません。 すでに計画されている一連のバッチに必要な棒鋼を事前に準備する場合、 機械周辺のスペースの管理はさらにデリケートになってきます。
このような状況を改善するために、 自動垂直タワー型保管システムを導入することで、 作業場の高さを活用し、 機械周辺のスペースを解放し、 より収益性の高い用途に使用することができます。
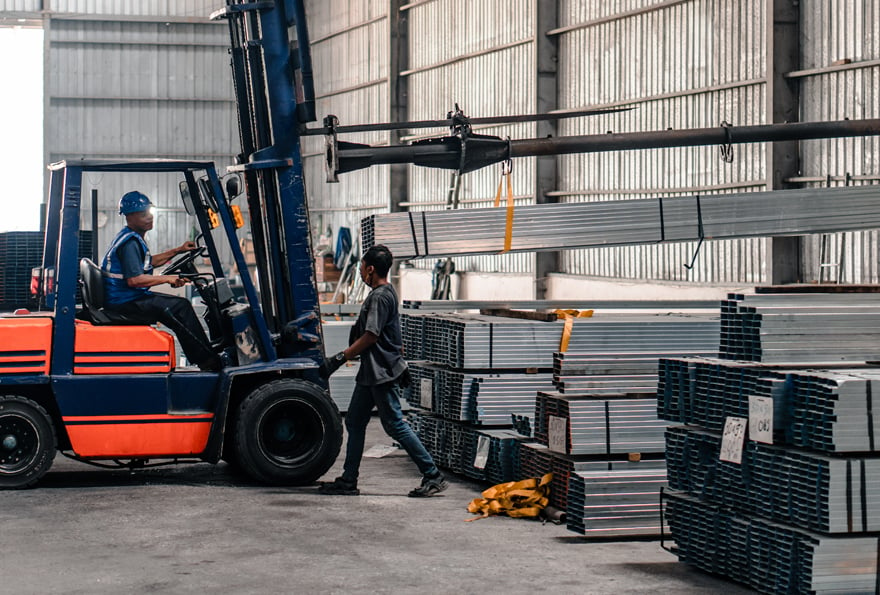
リアルタイムでの材料在庫管理
保管システムと会社の管理システムを連動させることで、 (機械統合の利点に加え)材料の在庫がモニターされ、 生産計画をより良く、 柔軟に管理することができます。
バッチ処理の終了時には、 ローダーから取り出されずに使用されなかったパイプがクレートに戻され、 適切に再計数され、 クレートはタワー内のラックに戻されます。
様々なクレートにどれだけの材料があるかを正確に把握することで、 パイプ貯蔵システムの定期的な充填を最適化し、 様々な材料管理戦略を評価し、 オフィスから計画を管理することが可能になります。
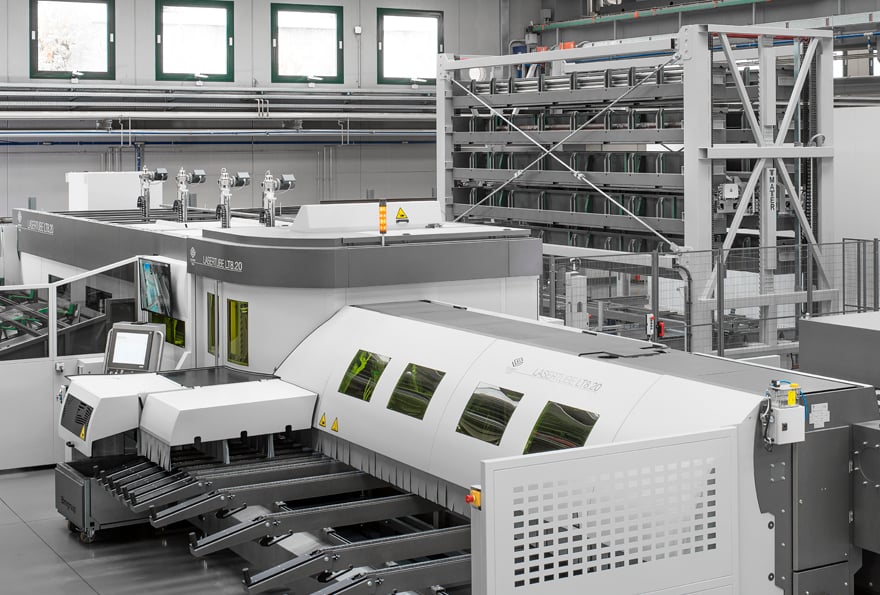
材料を保護する
他の多くの活動が周囲で行われる中、 重く扱いにくいパイプの束を中央保管システムから機械まで手動で往復させることは、 オペレータにとって不便で危険な作業になり得るだけでなく、 パイプの表面品質に影響を与える可能性があります。
たとえパイプの持ち上げ方や支え方だけが原因であっても、 バーの取り扱いにおける注意や配慮が、 キズや荷崩れを避けるために十分でない場合があります。
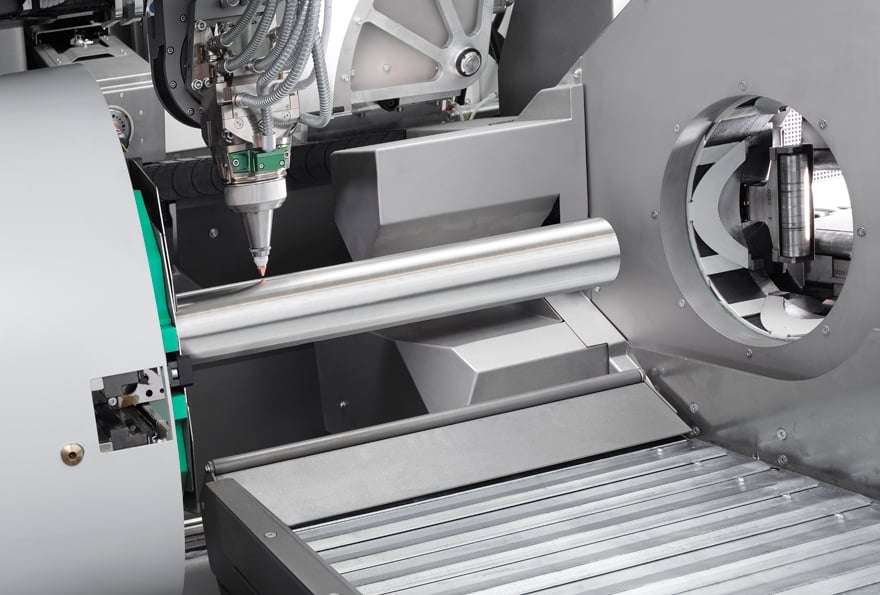
パイプに蓄積されたそうした傷は、 生産と材料の浪費の原因となります。 さらに重要なのは、 数量が限られている場合です。
パイプの自動タワー保管システムは、 加工するパイプをより保護された空間に保管し、 取り扱いを最適化して欠陥を最小限に抑えることで、 表面品質を維持するのに役立ちます。
オペレーターの安全性を高める
理由は同様ですが、 オペレーターやシステム周辺の人々にとって手動で行う危険性のある作業に関して、 さらに重要なことがあります。
完全自動化された積み下ろしにより、 貯蔵システムは、改善された原材料のロジスティクスを活用し、 最適な 「内部交通」 条件のもと、 一日のうちの正確な時間に充填することができます。
もはや、 手段や資源の継続的かつ断片的な関与はなく、 計画された一連のバッチのための準備という単一フェーズが存在するのです。

無人自動加工における継続性・信頼性の確保
バッチ間のマシンセットアップ時間の短縮により、 小ロットでの大量生産が可能になります。
自動化された塔載装置により、 無人加工が可能となり、 コストダウンと生産性の向上を実現します。
ミスの可能性を排除し、 オペレーターの経験値から独立することで、 さらなる効率性と時間およびコスト見積りの信頼性を実現します。
結論
競争力を維持することがますます必要になっている今日、 個々の工程の効率を高め、 材料処理や在庫管理における社内物流を簡素化し、 入手困難な専門労働者の高コストを抑制しつつ、 高い安全性と保護水準を保つためのソリューションが常に模索されています。
パイプや棒材の加工におけるタワー型保管システムの使用は、 この方向に向かうソリューションであり、 機械からの生産データの生成と詳細な分析、材料と人員の流れの監視、 生産の柔軟性を高めるためのデータの相互接続と交換が可能な生産システムといった他のサービスと組み合わせるとさらに効果的です。
パイプとセクションバーの自動保管システムは、 競争力の源泉が単にリソースと人件費の削減だけでなく、 新たに出現したインダストリー 4.0の技術的可能性を最大限に活用することにあることを意味しています。
パイプ加工機選定ナビを運営するBLM Group Japanでは、 実機見学やテストカットサービスを行っていますのでお気軽にお問い合わせください。