パイプレーザー 加工とシートレーザー加工の違いは?
この記事では、 パイプレーザー 加工とシートレーザー切断の主な違いについて説明します。シートレーザー切断から パイプレーザー 切断に、またはその逆に切り替えたいと考えている人が知っておくべきいくつかの基本的な基準があります。
目次
シートと パイプレーザー 切断は、似て非なるもの
レーザーカッティングは、製造業では何も新しいものではありません。数十年にわたり、より高性能な自動化システムを開発・販売してきた結果、他の成熟した技術とは異なり、「コモディティ化」、つまりこの技術に対する認識と使用における文化的転換の段階へと向かっていると言えるでしょう。
数年前、レーザー切断システムは、その初期購入価格だけでなく、オペレーターのトレーニングや、長期的かつ日常的に生産性とシステムの可用性を確保するために従わなければならない一定のメンテナンスプロトコルのために大きな投資を必要としました。
ファイバーレーザー光源の普及、自動化の進展、自動化装置とレーザー部品の標準化により、状況は大きく変わりました。
競争が激化していることもあり、初期投資額は徐々に減少していますが、統合されたセンサーを多用した結果、必要なトレーニングや経験が大幅に減少しています。工場の稼働率を100%に近づける診断・予防保全システムも、あと少しで実現できそうです。
「迅速・簡単」競争の結果、カッティングシステムはますます似通ったものになっていくでしょう。例えば、最もポピュラーなコピー機。コピー機の品質は標準化され、「コピー1枚あたりのコスト」(私たちの場合は部品単価に相当)だけが注目され続けています。
今後、メーカーが技術的な特徴やソリューションで差別化を図ることはますます難しくなり、レーザー切断システムにおける付帯サービス(包括保証、遠隔・予防保守・診断ツール、従量制契約、レンタル、買い取り契約など)の役割がますます顕著になると思われます。
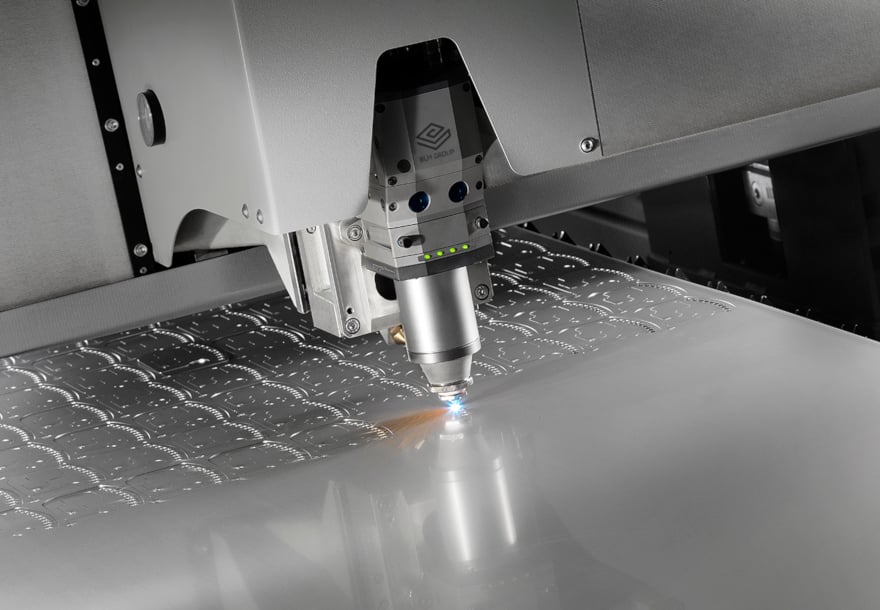
エンドユーザーにとって有利なこのシナリオは、シートレーザー切断システムのメーカーにとって確実に近い。競合他社が多く、技術的な内容が徐々に平準化されているため、メーカーは(他に選択肢がない場合は)利幅を減らすか、有形無形の追加機能を統合する方向に進んでいます。
絶対的な技術的ベンチマークとなるブランドはまだ少数ではありますが、一方で、新しいアプリケーションニッチに常に支えられている需要をボトムアップで攻めようとする、大胆な新規参入者が増えてきています。
パイプレーザー 加工分野も同じような進化を遂げることが予想されます。しかし、簡素化とコスト削減への大きなステップにもかかわらず、技術的な内容ではまだ差別化が図られています。
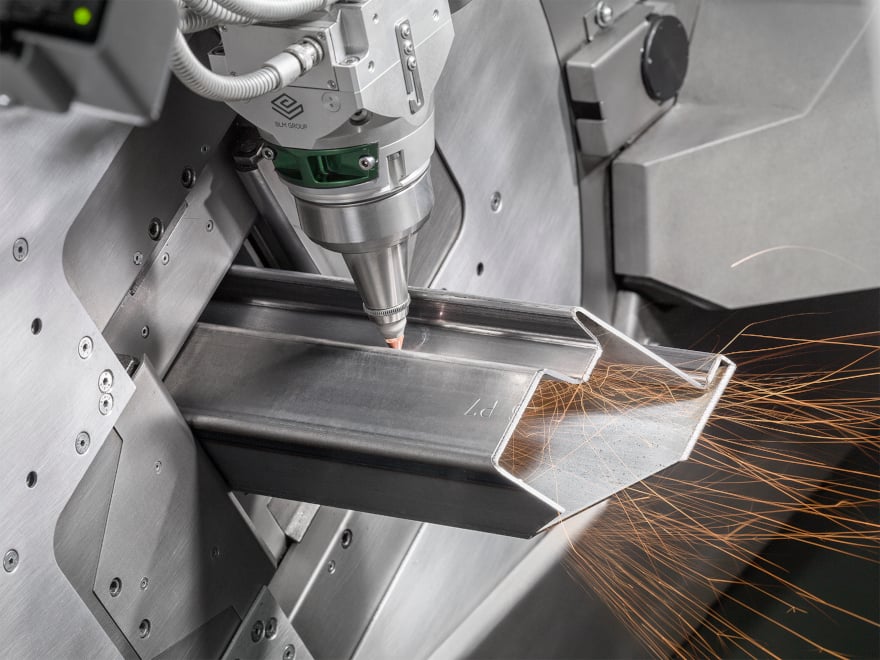
パイプレーザー加工機は、老舗メーカーと新興メーカーで性能に大きな差があり、投資水準と技術的価値の相関関係がまだ強いことを示しています。
この差は今後縮まっていくと予想されますが、今選択を迫られている人たちは、いくつかの要素を知っておくことをお勧めします。
そこで、パイプ切断機とシート切断機とでは、どのような点で評価が異なるのか、より複雑なのかを分析してみます。
パイプレーザー は加工中パイプも動く!
パイプレーザー切断システムを見たとき、まず目に飛び込んでくるのは、材料が加工中ずっと動いているということです。
板材の場合とは異なり、パイプは切断エリアに搬入された後、高速で回転し、時には高加速しながら、切断中に移動し続けます。
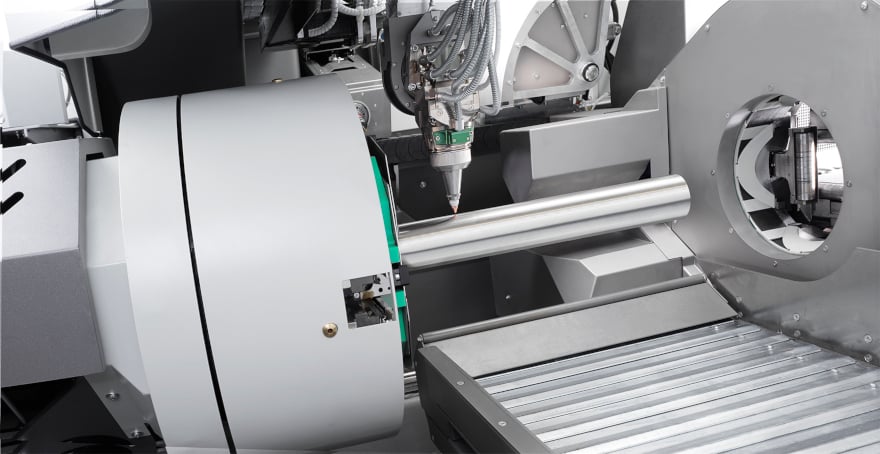
このことは、システムの信頼性と生産性の両方に重要な影響を及ぼします。
細く柔軟なパイプは、適切にガイドされないと曲がったり詰まったりする傾向があり、頻繁に中断するリスクが高まります。重いパイプは衝撃や振動で機械にストレスを与え、システムの効率を長期間維持するためには、機械的な堅牢さと特定のソリューションが必要です。
大口径パイプレーザー切断について、もっと知りたくありませんか?お客様のニーズに最適な機械の仕様はこちらです。
特殊断面 での パイプレーザー 切断:1つのソリューションで多くの形状を実現
板金と比較した場合のパイプのもう一つの特徴は、膨大な数の異なる形状、断面、プロファイルが利用できることです(材料と厚みの多様性は板金加工と同等です)。
初期のシステム(30年以上前のADIGE・BLMGROUP パイプレーザー 加工機)で加工可能だった最も単純な丸、四角、長方形のパイプから、より複雑で厚みが変化し、凹型のプロファイルを持つものに至るまで、様々なものがあります。
それぞれの断面や形状は、積み込みからハンドリング、レーザー出力を正しく調整して一貫した高品質の切断(下記参照)、搬出まで、正しく管理するための課題を提起しています。
軽量で短いパイプから、構造分野で使用されるような大型で重いセクション(数メートルの長さに切断)まで、加工が常に信頼でき、持続できるようにするために、システムが備えていなければならない機能やソリューションが数多くあります。
また、加工する形状によっても違いが出てきます。例えば、マイクロジョイントを正しく挿入することで、他の方法では実現不可能なパーツを作ることができます。パイプレーザー加工機用のパーツプログラムを作成する際に、専門家でなければ検知・防止できないような好ましくない事態からシステムを保護し、システムを正しく使用できるようにするために、自動管理が可能であれば、パーツの実現性を高めることができます。
言うまでもなく、平板切断の管理は(少なくともほとんどのシステムで)はるかに制限されます。厚さ、材質、切断の種類、形状に関係なく、部品は切断されたシートの中に静止したまま保持されます。
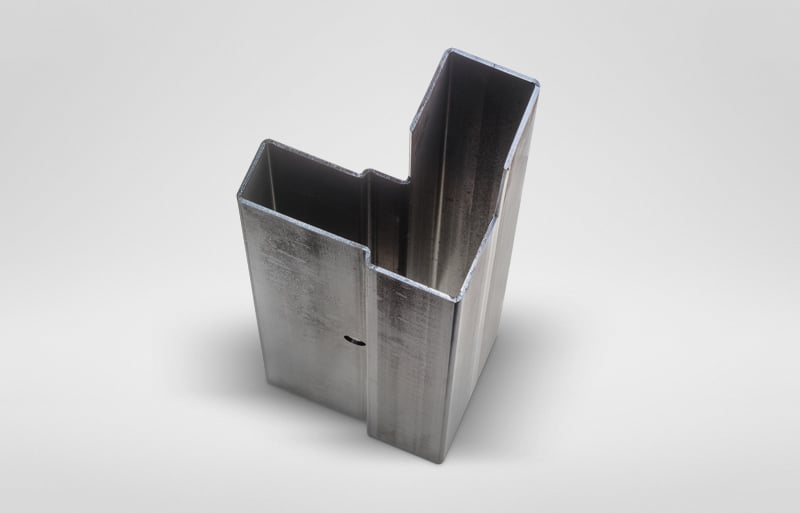
ネスティングのアルゴリズム:無駄を省いたところから「利益」が溜まる
金属価格が高騰する中、原材料を使い切れず、余分なスクラップが発生して廃棄(せいぜいリサイクル)されるのは、もはや許されないことである。
また、製造する部品の数を超えて余分に材料を購入することも考えられません。プロセスパラメーターを最適化し、生産性と切断品質の適切なバランスをとるための最初の試行(アプリケーション分野と独自のスタイルに応じて常に主観的)を除けば、いったん生産が開始されれば、利用可能な材料を最大限に活用できるようにしなければならないのです。
シートの世界では、ネスティングやコンパクションのアルゴリズムによって、すべてのパーツを可能な限り近づけるように配置・回転させることで、これを実現しています。こうすることで、無駄を省き、より多くのパーツを1枚のシートに収めることができます。
パイプも同様ですが、少し複雑な点があります。パイプは立体的であるため、特にパーツが互いに異なる場合、圧縮するのがより複雑になります。

平凡なソリューションから最適なソリューションに移行することで、何メートルものパイプを節約することができます。その差(つまり節約額)は、たとえ単一バッチであっても、大きくて厚い断面では大きなものになります。最先端の成形ソリューションがあれば、どのような生産構成であっても、莫大な利益を得ることができるのです。
汚れたパイプや不完全なパイプの切断:あらゆる条件下でリードする
パイプ業界で働く人なら誰でも、パイプ製造における幾何公差、ねじれや軸曲げの問題、表面の汚れや錆などは、オペレーターが対処する必要がある問題であることを知っています。
これらの問題のうち、板金に影響するものはごくわずかです。したがって、パイプから一定の品質で、妥当な時間内に、無駄なく部品を得ることが、決して簡単ではないことは容易に理解できます。そのためには、パイプの形状のばらつきを認識・補正し、汚れや錆を効果的に処理できる技術的なソリューションが再び必要となる。また、厚みが一定でない部分(溶接部など)や曲率が変化する部分(深く急な凹みがある特殊な部分など)での火傷や切断の損失を避けるため、レーザー出力自体を経路上のすべての地点で前進速度に応じて正しく調整することが望ましいと言えます。
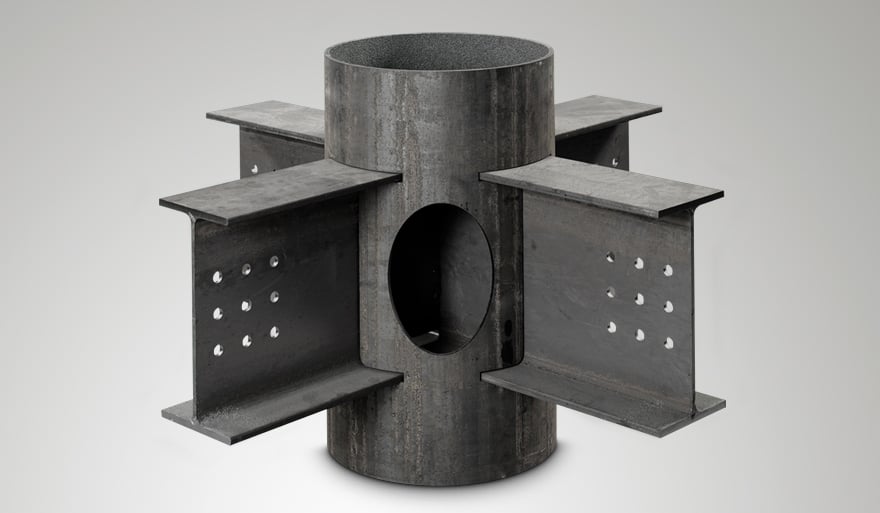
パイプレーザー 光源:より少ない出力で、より大きな制御が可能!
もう一つ、板金とパイプの世界の重要な違いは、切断装置に搭載されるレーザー光源のパワーにある。
最近、板金装置のレーザー光源が極端に大きくなっているのを見かけます。(15kW以上、最高30kW!)出力向上が生産性の向上と板金の最大加工可能厚さの増加につながることは間違いない。しかし、パイプの場合はそうならなかった。なぜでしょうか?
その答えは、やはり材料の形状にあります。一つは、平板のように高速で長距離を移動することができないこと。次に、パイプの場合、加工できる厚みの範囲がかなり限定される(厚い材料では、設備で許容される重量の限界にすぐに達してしまう)。さらに、チューブ自体が閉じた形状、つまり切断する側と反対側に一面があるため、切断および未切断の壁の火傷や過熱を防ぐために使用できる最大電力が制限されます。
シートには反対側の壁があるという問題がないため、厚みを超えたら(うまく管理すれば)切断に使用する電力は支持グリッドに分散されます。
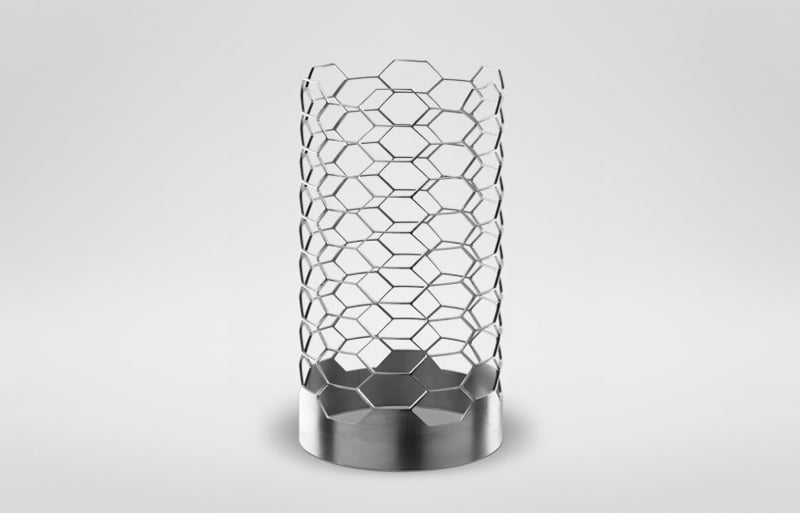
パイプレーザー 加工は 2+1=3とは限らない!
2Dレーザー切断システムを3Dに変換するには、軸を追加するだけでは十分ではありません。この特殊な切断方法は、板金ではあまり一般的ではありませんが(一部の例外を除いて)、一方で、何が必要で何が実現できるかを知っていれば、パイプのために考慮すべき機会でもあります。レーザービームを材料表面に対して傾けて切断することで、穴の面取り、エッジや端部の傾斜、パイプ間の正確な接合や支持を実現し、後の溶接を容易にします。
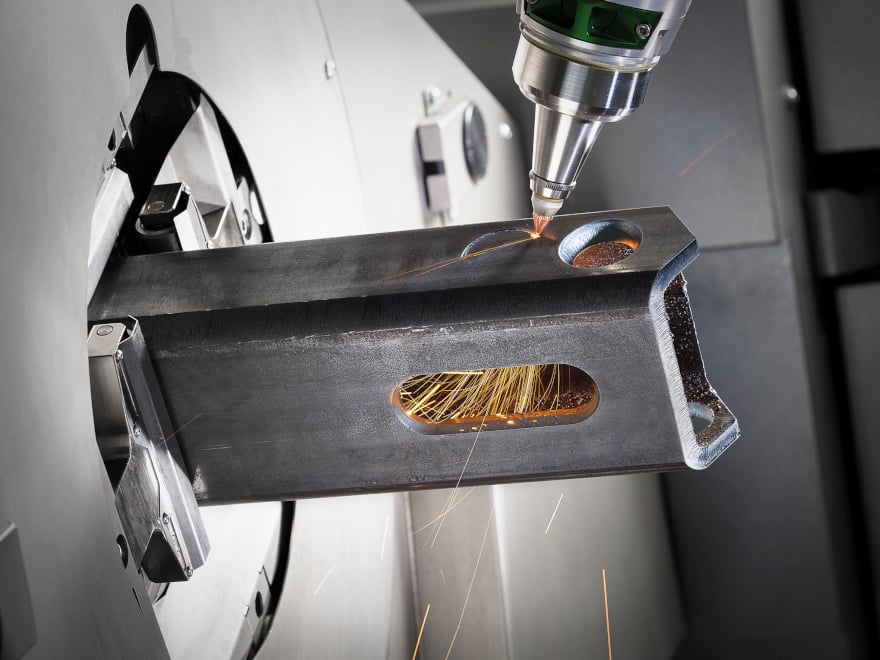
パスの各ポイントで傾斜角が変わると、切断される厚みが変わり、それに伴ってレーザーパラメーターも変更しなければなりません。これらの変更を数値制御と機械の統合アルゴリズムによって自動的かつ堅牢に管理できれば、3Dカッティングが提供するすべての機会を活用することができるのですが、そうでなければ、メリットよりも手間がかかることになります。
パイプレーザー 加工とシートレーザー加工の主な違い:結論
最後に、パイプレーザー切断システムの選択を複雑にし、シートシステムの選択とは異なるものにし得る要素をいくつか見てきました。アプリケーションの分野や生産性、持続可能性への期待によって、他にも多くの要素があるかもしれません。
しかし、経験豊富で信頼できるサプライヤーを信頼し、長期にわたって価値をもたらし、企業の成長に貢献する投資を行えばよいのです。
パイプ加工機選定ナビを運営するBLM Group Japanでは、実機見学やテストカットサービスを行っていますのでお気軽にお問い合わせください。